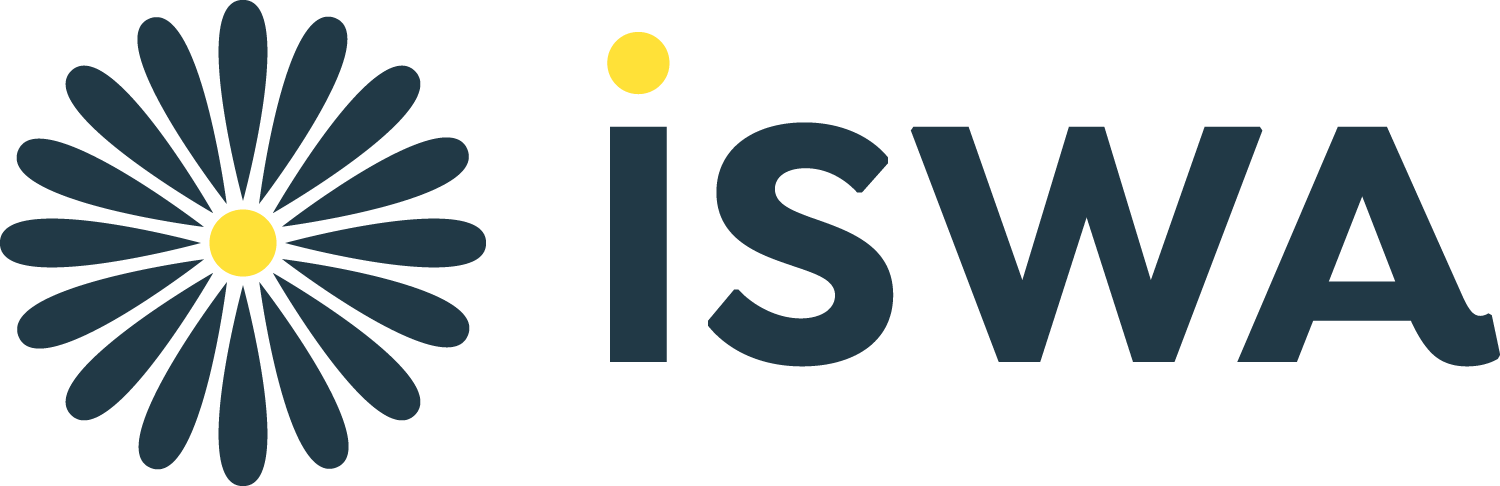
Inventory management involves the purchase, storage, use, packaging, and shipment of goods. This helps ensure that customers are satisfied with the products a company has. It allows companies monitor buyer trends and improves speed to market. It is essential to know how to efficiently use inventory to ensure effective inventory management.
Inventory management is the process for buying, storing or using goods and then packaging them to ship them.
Management of inventory is an essential part of running any business. It is an integral part in running a successful business as it can save a company from financial disasters. Managing inventory can be difficult, especially if your business has several locations. For example, you might have multiple warehouses. This means you will need to be aware of stock levels in every location. While managing inventory can seem time-consuming, it is crucial for your company's success.
There are many options for managing inventory. One method to manage inventory is the economic order quantity (EOQ). To determine how much inventory a company should own, this measurement considers the total cost of production as well as consumer demand. The EOQ is a tool that can be used to help businesses remain profitable and make more cash.
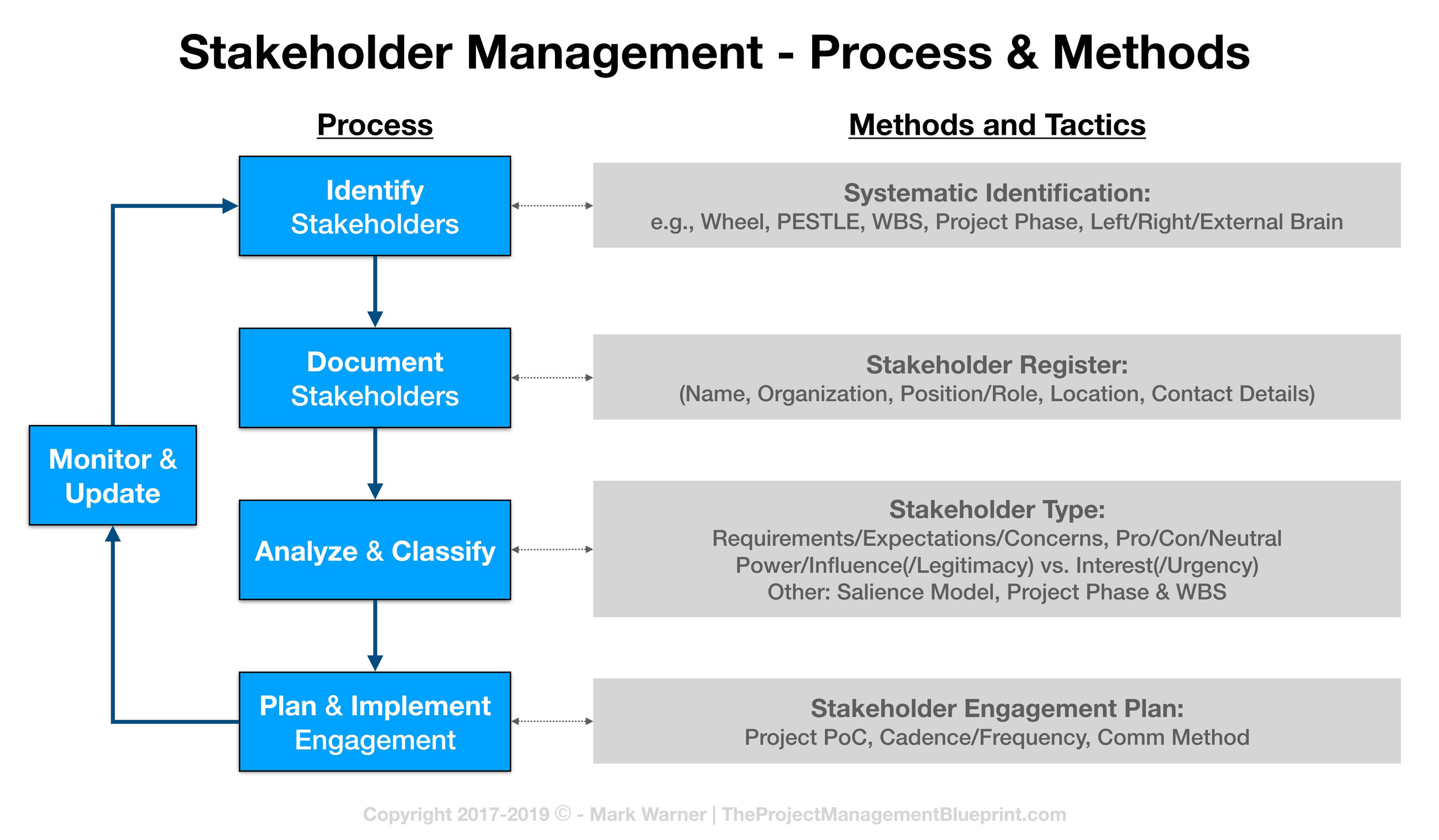
It assures that finished goods are always available
Effective inventory management can help companies to differentiate themselves from the competition. It involves sorting products and storing them according to customer demand. Cross docking and dropshipping are possible. Software systems can be used to monitor inventory levels. A business can monitor its inventory levels using the right software system to maximize inventory planning. Inventory management usually begins when a customer places a purchase, either online or in a physical location.
Another type focuses on inventory management is the management of raw materials. These are purchased from another company or manufactured in-house. This inventory may include parts that are being manufactured, such as nuts or screws. It may also include work-in progress inventory such as parts that are needed to pack finished goods or perform maintenance repairs. It can also include office supplies like paper or pencils.
It helps companies track buyer trends over the course of time.
Inventory management is the process of tracking the items a company has on hand. It involves reviewing this data on a regular basis to determine which items should be stockpiled and when. This is a crucial step as it can help companies spot patterns in buyer behavior. It can help you identify shrinkage issues by keeping track of your inventory.
Companies also benefit from inventory management to identify and remove obsolete products. These products are items that customers have discontinued buying or are at the end of their useful life. Other problems associated with inefficient warehouse organization include inadequate signage, inadequate walking space, and unsafe storage conditions. You can also use the inventory turnover ratio (ITR), to see how often a company replaces its inventory. The higher the ITR, the more likely the company is to sell the majority of its inventory during a cycle.
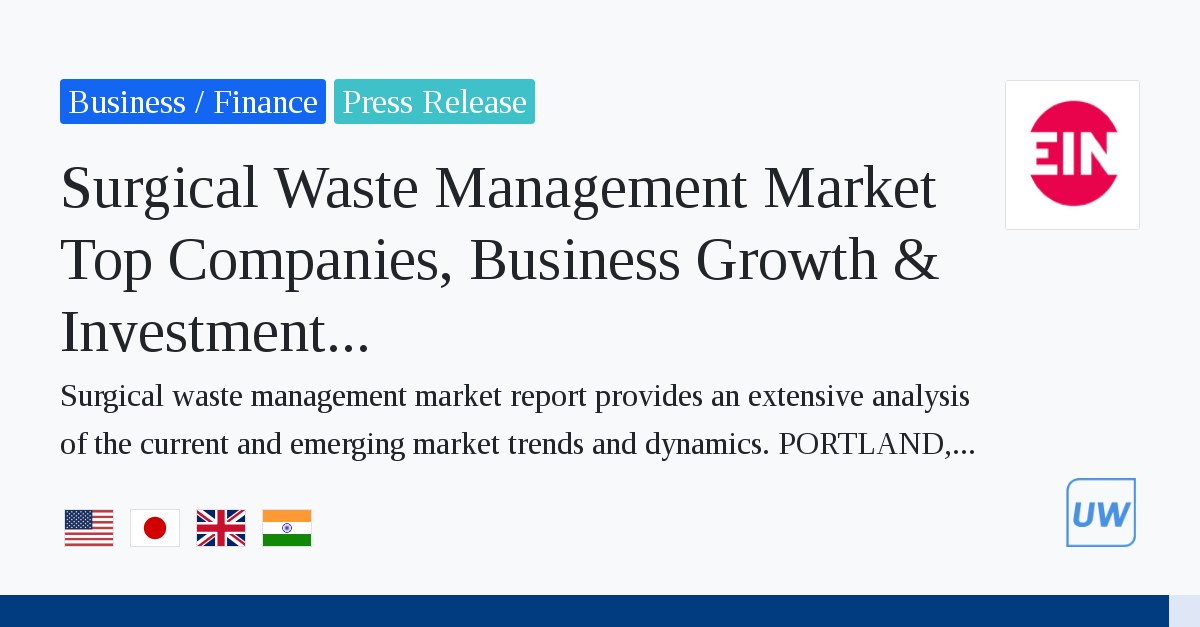
It speeds up the time it takes to get to market
Inventory management allows companies and organizations to ship items more quickly and ensures that they have sufficient stock. It reduces the possibility of missing stock items or cancelled orders. Stock outages can cause customers frustration. Inventory management can help prevent this.
It is crucial for any business to manage its inventory. It is a complicated task that requires many decisions. Excel formulas might be used by small companies to keep track and determine reorder point stock. Enterprise resource planning software can be used for larger businesses. Specialized SaaS applications may be available for large corporations.
FAQ
How does a manager motivate their employees?
Motivation is the desire for success.
Engaging in something fun can be a great way to get motivated.
You can also feel motivated by making a positive contribution to the success in the organization.
You might find it more rewarding to treat patients than to study medical books if you plan to become a doctor.
Another source of motivation is within.
You might feel a strong sense for responsibility and want to help others.
You may even find it enjoyable to work hard.
Ask yourself why you feel so motivated.
Next, think of ways you can improve your motivation.
What's the difference between Six Sigma and TQM?
The main difference between these two quality-management tools is that six-sigma concentrates on eliminating defects while total QM (TQM), focuses upon improving processes and reducing expenses.
Six Sigma is a method for continuous improvement. It emphasizes the elimination of defects by using statistical methods such as control charts, p-charts, and Pareto analysis.
This method attempts to reduce variations in product output. This is done by identifying root causes and rectifying them.
Total quality management is the measurement and monitoring of all aspects within an organization. It also includes the training of employees to improve performance.
It is often used to increase productivity.
It seems so difficult sometimes to make sound business decisions.
Businesses are complex systems, and they have many moving parts. Their leaders must manage multiple priorities, as well as dealing with uncertainty.
It is important to understand the effects of these factors on the system in order to make informed decisions.
This requires you to think about the purpose and function of each component. Next, consider how each piece interacts with the others.
You should also ask yourself if there are any hidden assumptions behind how you've been doing things. If you don't have any, it may be time to revisit them.
Asking for assistance from someone else is a good idea if you are still having trouble. They may see things differently from you and have insights that could help you find a solution.
Six Sigma is so well-known.
Six Sigma is easy and can deliver significant results. It can also be used to help companies identify and focus on the most important aspects of their business.
What is Kaizen?
Kaizen is a Japanese term meaning "continuous improvement." It is a philosophy that encourages employees to constantly look for ways to improve their work environment.
Kaizen is based on the belief that every person should be able to do his or her job well.
What is the difference in a project and program?
A project is temporary; a program is permanent.
Projects usually have a goal and a deadline.
It is often carried out by a team of people who report back to someone else.
A program is usually defined by a set or goals.
It is often done by one person.
Statistics
- As of 2020, personal bankers or tellers make an average of $32,620 per year, according to the BLS. (wgu.edu)
- 100% of the courses are offered online, and no campus visits are required — a big time-saver for you. (online.uc.edu)
- Our program is 100% engineered for your success. (online.uc.edu)
- The average salary for financial advisors in 2021 is around $60,000 per year, with the top 10% of the profession making more than $111,000 per year. (wgu.edu)
- The BLS says that financial services jobs like banking are expected to grow 4% by 2030, about as fast as the national average. (wgu.edu)
External Links
How To
What is Lean Manufacturing?
Lean Manufacturing methods are used to reduce waste through structured processes. They were developed by Toyota Motor Corporation in Japan during the 1980s. The goal was to produce quality products at lower cost. Lean manufacturing seeks to eliminate unnecessary steps and activities in the production process. It is composed of five fundamental elements: continuous improvement; pull systems, continuous improvements, just-in–time, kaizen, continuous change, and 5S. The production of only what the customer needs without extra work is called pull systems. Continuous improvement is the continuous improvement of existing processes. Just-in-time refers to when components and materials are delivered directly to the point where they are needed. Kaizen stands for continuous improvement. Kaizen can be described as a process of making small improvements continuously. The 5S acronym stands for sort in order, shine standardize and maintain. These five elements can be combined to achieve the best possible results.
The Lean Production System
Six key concepts make up the lean manufacturing system.
-
Flow: The goal is to move material and information as close as possible from customers.
-
Value stream mapping- This allows you to break down each step of a process and create a flowchart detailing the entire process.
-
Five S’s - Sorted, In Order. Shine. Standardize. And Sustain.
-
Kanban - visual cues such as stickers or colored tape can be used to track inventory.
-
Theory of constraints: Identify bottlenecks and use lean tools such as kanban boards to eliminate them.
-
Just-in-time - deliver components and materials directly to the point of use;
-
Continuous improvement - incremental improvements are made to the process, not a complete overhaul.