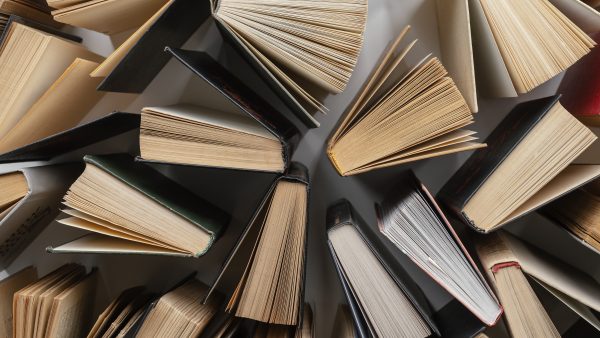
Strategic sourcing involves identifying and evaluating the best vendors for a given task. It involves many steps from market research and benchmarking to finding the right partners. The best vendor for the task is not enough. Strategic sourcing also requires that you consider return on investment. This involves looking at the costs and benefits of establishing a new supplier and the time it will take to save over time.
Market research
Market research agencies are able to unlock the potential of your business by identifying new markets, demographics, and other opportunities. They also help you develop concrete business strategies backed by data. These agencies do different types research. They include primary research (focus Groups), secondary research(review of published sources, identifying relevant publications) and data mining (data acquisition).
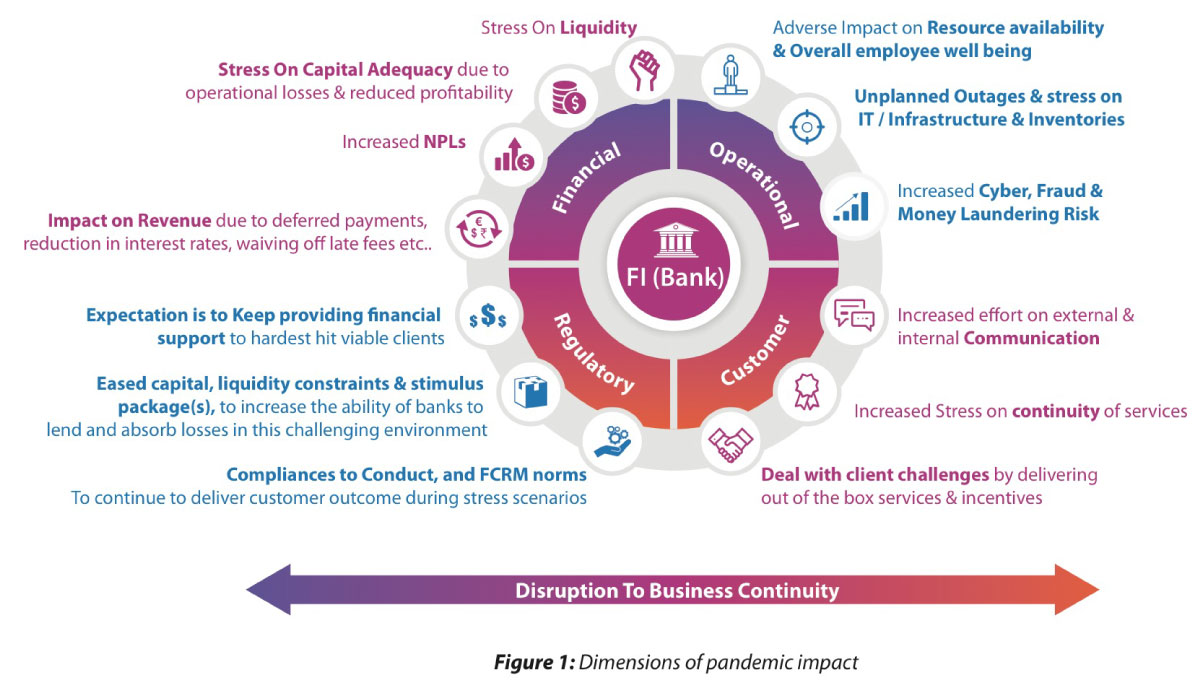
Forecasting
Forecasting is a key aspect of strategic sourcing. Forecasting can be used to help businesses predict demand. This can allow for shorter lead times, and improve customer trust. In addition, forecasting can eliminate the need for safety stock, which is excess inventory held to meet unforeseen demand. This helps to free up storage space as well as save time.
Partnerships:
Strategic sourcing is the process of forming partnerships with suppliers that can fulfill a specific need. These partnerships must be developed through a collaborative process. It is vital to establish trust and align yourself with the goals. A dedicated resource is required to ensure that successful partnerships lead to better business outcomes.
Finding the best partner
It is a crucial first step in any strategic sourcing project to identify the best partner. Before you finalize a strategic-sourcing contract, it's important to communicate and understand the capabilities of your suppliers. After a team of strategic sourcing professionals has chosen its perfect partner, they need to communicate their next steps with suppliers and follow their recommendations.
Cost analysis
Cost analysis is an important component of strategic sourcing. It helps companies understand their profit margins and determine whether they can lower costs by choosing a less expensive supplier. It can also compare the prices for components and assembled products. The results can be used to inform procurement teams about which components and assemblies they should buy or manufacture.
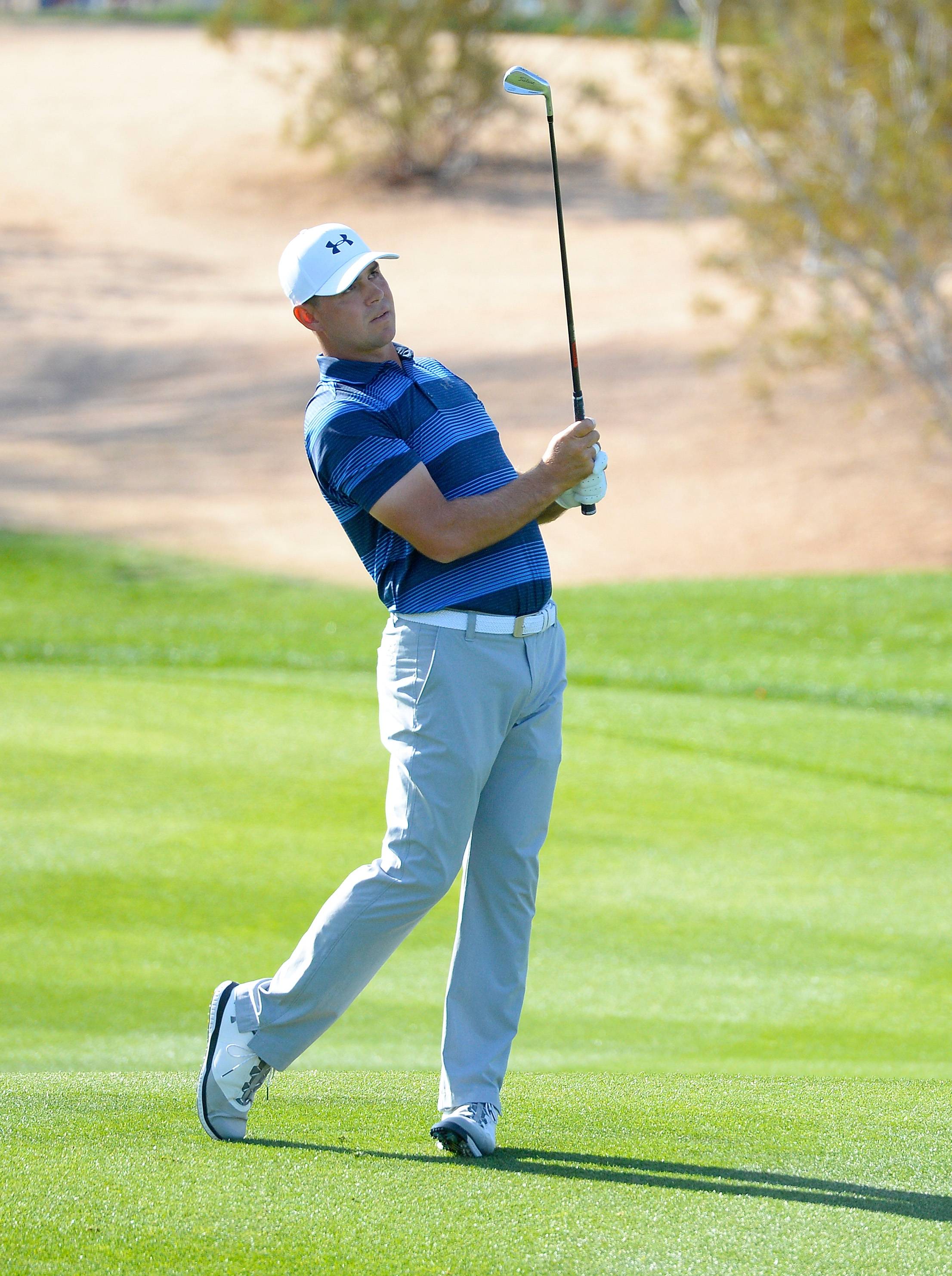
RFP technology
RFP technology plays an important role in strategic sourcing. The technology allows companies simplify their processes, and makes it easier to evaluate suppliers. By automating their evaluations, companies can save time as well as money. An RFP software tool can help reduce the time taken to shortlist suppliers. It also allows companies to maintain vendor profiles, which enable them to track changes and stay updated with new developments.
FAQ
What is the difference between management and leadership?
Leadership is about being a leader. Management is about controlling others.
Leaders inspire followers, while managers direct workers.
Leaders motivate people to succeed; managers keep workers on track.
A leader develops people; a manager manages people.
What is Six Sigma?
It's an approach to quality improvement that emphasizes customer service and continuous learning. This is an approach to quality improvement that uses statistical techniques to eliminate defects.
Motorola created Six Sigma as part of their efforts to improve manufacturing processes in 1986.
This idea quickly spread throughout the industry. Today, many organizations use six sigma methods for product design, production and delivery.
What is the difference between Six Sigma Six Sigma and TQM?
The major difference between the two tools for quality management is that six Sigma focuses on eliminating defect while total quality control (TQM), on improving processes and decreasing costs.
Six Sigma is a method for continuous improvement. This method emphasizes eliminating defects using statistical methods such p-charts, control charts, and Pareto analysis.
This method attempts to reduce variations in product output. This is done by identifying root causes and rectifying them.
Total quality management refers to the monitoring and measurement of all aspects in an organization. Training employees is also part of total quality management.
It is often used to increase productivity.
What are the five management process?
These five stages are: planning, execution monitoring, review and evaluation.
Planning means setting goals for the long-term. It includes defining what you want to achieve and how you plan to do it.
Execution is the actual execution of the plans. These plans must be adhered to by everyone.
Monitoring allows you to monitor your progress towards achieving your goals. Monitoring should include regular reviews of performance against goals and budgets.
Review events take place at each year's end. They give you an opportunity to review the year and assess how it went. If not, then it may be possible to make adjustments in order to improve performance next time.
After the annual review is complete, evaluations are conducted. It helps identify which aspects worked well and which didn't. It also provides feedback on the performance of people.
How do you manage employees effectively?
Managing employees effectively means ensuring that they are happy and productive.
It is important to set clear expectations about their behavior and keep track of their performance.
Managers must be clear about their goals and those of their teams in order to succeed.
They must communicate clearly with their staff. They need to communicate clearly with their staff.
They also need to keep records of their team's activities. These include:
-
What was achieved?
-
How much work were you able to accomplish?
-
Who did it and why?
-
What was the moment it was completed?
-
Why was this done?
This information can help you monitor your performance and to evaluate your results.
What are the steps to take in order to make a management decision?
Managers are faced with complex and multifaceted decisions. It involves many factors, including but not limited to analysis, strategy, planning, implementation, measurement, evaluation, feedback, etc.
It is important to remember that people are human beings, just like you. They make mistakes. As such, there is always room for improvement, especially if you're willing to put forth the effort to improve yourself first.
We explain in this video how the Management decision-making process works. We discuss different types of decisions as well as why they are important and how managers can navigate them. Here are some topics you'll be learning about:
What are your main management skills
No matter if they are running a local business or an international one, management skills are vital. These include the ability and willingness to manage people, finances as well resources, time and space.
You will need management skills to set goals and objectives, plan strategies, motivate employees, resolve problems, create policies and procedures, and manage change.
As you can see, there's no end to the list of managerial duties!
Statistics
- Our program is 100% engineered for your success. (online.uc.edu)
- Your choice in Step 5 may very likely be the same or similar to the alternative you placed at the top of your list at the end of Step 4. (umassd.edu)
- The profession is expected to grow 7% by 2028, a bit faster than the national average. (wgu.edu)
- This field is expected to grow about 7% by 2028, a bit faster than the national average for job growth. (wgu.edu)
- As of 2020, personal bankers or tellers make an average of $32,620 per year, according to the BLS. (wgu.edu)
External Links
How To
How can you implement the Kaizen technique?
Kaizen means continuous improvement. This term was first used by Toyota Motor Corporation in the 1950s. It refers to the Japanese philosophy that emphasizes continuous improvement through small incremental changes. It's a team effort to continuously improve processes.
Kaizen is one of the most effective methods used in Lean Manufacturing. Kaizen is a concept where employees in charge of the production line are required to spot problems during the manufacturing process before they become major issues. This increases the quality of products and reduces the cost.
Kaizen is the idea that every worker should be aware of what is going on around them. Correct any errors immediately to avoid future problems. So, if someone notices a problem while working, he/she should report it to his/her manager.
Kaizen is based on a few principles. Start with the end product, and then move to the beginning. For example, if we want to improve our factory, we first fix the machines that produce the final product. First, we fix machines that produce components. Next, we fix machines that produce raw material. And finally, we fix the workers who work directly with those machines.
This is why it's called "kaizen" because it works step-by-step to improve everything. We finish fixing the factory and then go back to the beginning. This continues until we achieve perfection.
How to measure kaizen's effectiveness in your business is essential to implement it. There are many methods to assess if kaizen works well. One of these ways is to check the number of defects found on the finished products. Another way is to check how much productivity has grown since kaizen was implemented.
To determine if kaizen is effective, you should ask yourself why you chose to implement kaizen. Did you do it because it was legal or to save money? It was a way to save money or help you succeed.
Suppose you answered yes to any of these questions, congratulations! Now you're ready for kaizen.