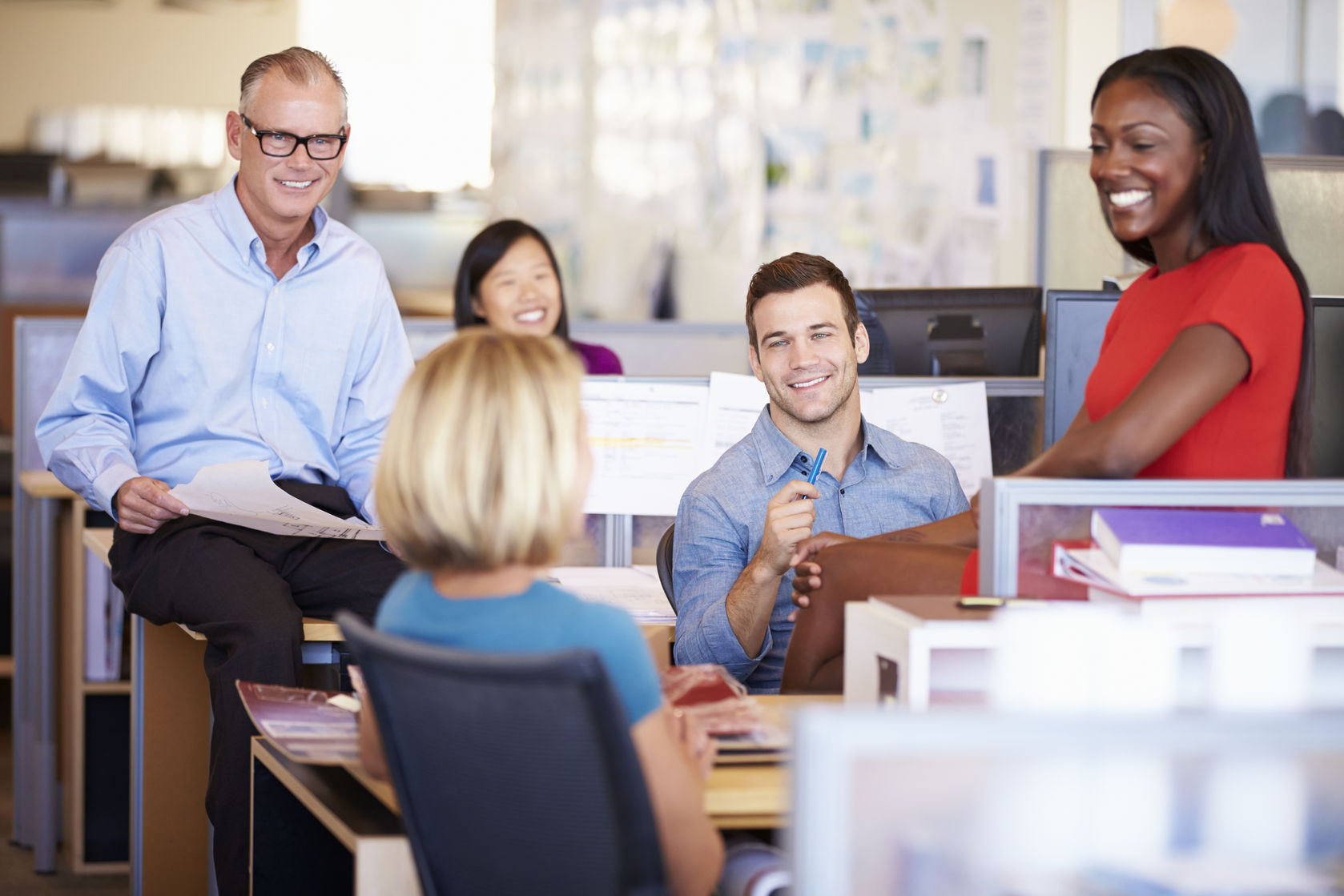
A key aspect of any construction project is the management of construction. A construction manager represents the owner's interests and oversees all aspects of the project. He or she is responsible for ensuring that the project is completed within budget and on time. To meet the needs of the owner, he or she works closely with the general contractor and architect. A construction manager should be well-versed in construction practices and methods to be successful in his or her role.
Pre-construction
The key component of the construction process is pre-construction management. It includes the planning, estimation, and management of all aspects of a project. It involves working with all stakeholders to understand the design intent, end user needs, and project scope. Ultimately, the aim is to complete a project on time and within budget.
The client and their construction partner will work together to develop detailed drawings and schedules, budgets, manpower projections, and other details. It is essential to maintain regular communication during this phase as it allows you to spot potential construction problems and help you resolve them. It also ensures the project follows the initial schedule.
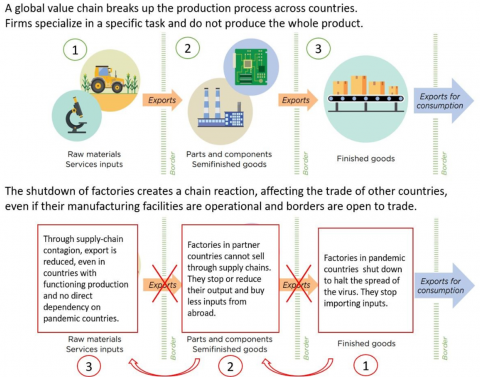
Hire subcontractors
Subcontractors are an important part of construction management. Subcontractors are a crucial part of a project's success and can play a vital role in it. Subcontractors need to be selected carefully in order to avoid any delays or problems. They should have a proven track record and a reputation for quality work.
While subcontractors may be independent contractors, they still have the same legal protections available as employees. Therefore, it is important that you understand the legal aspects involved in subcontracting. Subcontractors, being independent contractors, are subject to the same tax obligations that a general contractor. This can lead to them being liable for paying back taxes and employee benefit.
Closeout of construction project
It is vital that a construction project closes successfully. This will have a positive impact on the financial and operating health of the owner. Therefore, it is crucial to plan ahead and coordinate with all relevant parties early in the construction process. There are many key points to be aware of. These steps will reduce disputes and help you avoid problems. Here are some tips for planning a successful project closing.
It can take a long time to close out a construction project. This process includes punch lists, final inspections, as-built submissions, and the preparation of punch lists. A well-planned finalization will save time and money. It will also reduce stress for all involved, including clients and employees.
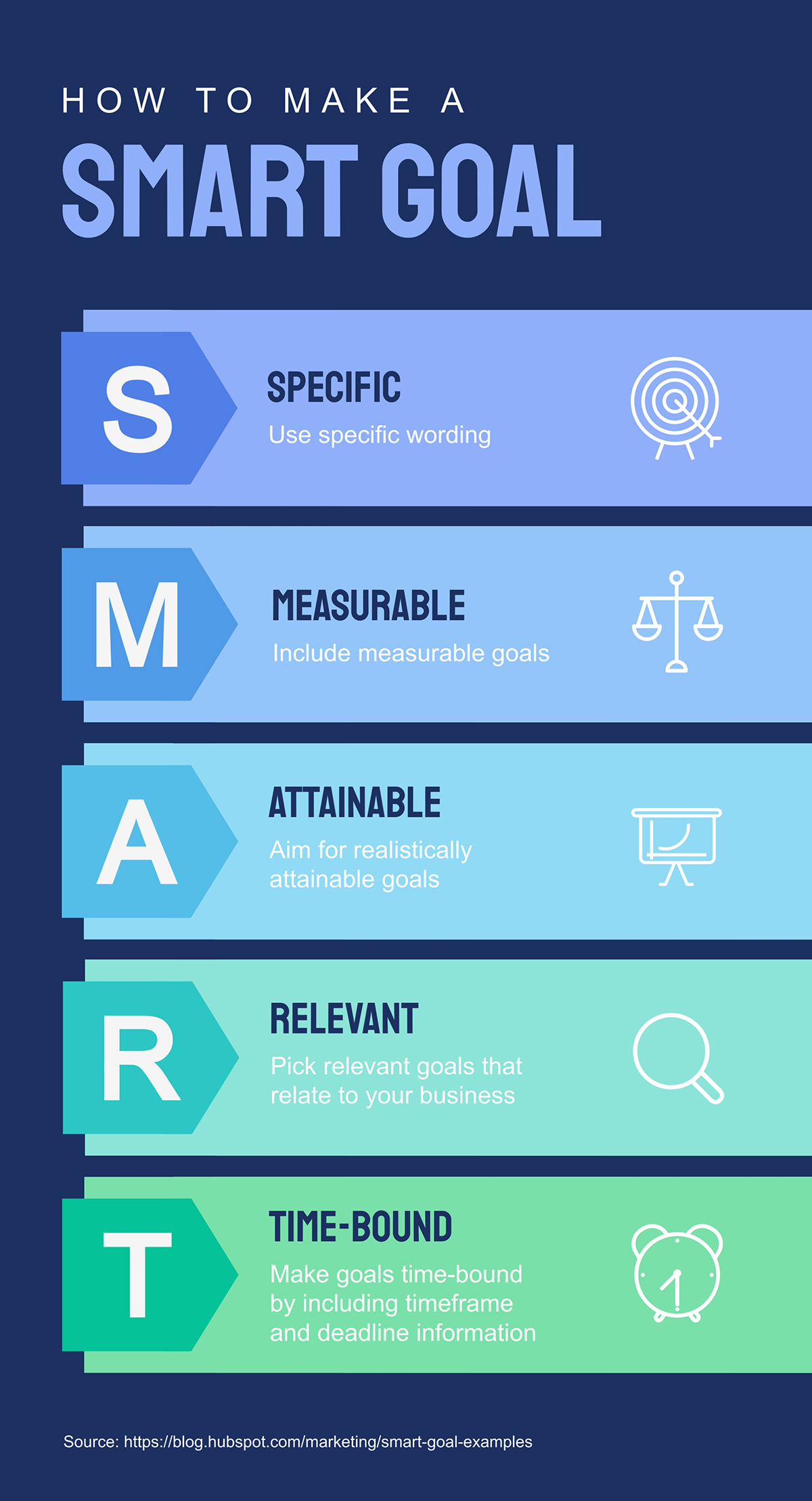
Cloud-based Software
Software that manages construction can increase your ROI. These applications can not only automate routine tasks but also integrate with other business apps. These apps can be used to monitor and manage budgets and schedules, make changes and get information from subcontractors. Many of these apps can be integrated into CRM and takeoff software. They can manage a wide range of project types.
Cloud-based construction administration software has another advantage: it can adapt quickly to changing fields needs. Cloud-based software makes it easy to instantly access the most recent features and updates. This means that updates are available immediately and there is no waiting.
FAQ
What are the three basic management styles?
These are the three most common management styles: participative (authoritarian), laissez-faire (leavez-faire), and authoritarian. Each style has its own strengths and weaknesses. Which style do your prefer? Why?
Authority - The leader is the one who sets the direction and expects everyone in the organization to follow it. This style is best when the organization has a large and stable workforce.
Laissez-faire - The leader allows each individual to decide for him/herself. This approach works best in small, dynamic organizations.
Participative: The leader listens to everyone's ideas and suggestions. This style works best in smaller organizations where everyone feels valued.
How does Six Sigma work
Six Sigma employs statistical analysis to identify problems, measure them and analyze root causes. Six Sigma also uses experience to correct problems.
First, identify the problem.
Next, data will be collected and analyzed to determine trends and patterns.
The problem is then rectified.
Finally, the data are reanalyzed in order to determine if it has been resolved.
This cycle continues until the problem is solved.
What is the main difference between Six Sigma Six Sigma TQM and Six Sigma Six Sigma?
The main difference between these two quality management tools is that six sigma focuses on eliminating defects while total quality management (TQM) focuses on improving processes and reducing costs.
Six Sigma is a method for continuous improvement. It emphasizes the elimination or minimization of defects through statistical methods such control charts and p charts.
This method aims to reduce variation in product production. This is accomplished through identifying and correcting root causes.
Total quality management includes monitoring and measuring all aspects of an organization's performance. This includes training employees to improve their performance.
It is often used as a strategy to increase productivity.
What's the difference between leadership & management?
Leadership is about influencing others. Management is all about controlling others.
A leader inspires others while a manager directs them.
A leader motivates people to achieve success; a manager keeps workers on task.
A leader develops people; a manager manages people.
Why is project management important for companies?
Project management techniques are used to ensure that projects run smoothly and meet deadlines.
This is because many businesses depend heavily upon project work to produce products and services.
These projects require companies to be efficient and effective managers.
Without effective project management, companies may lose money, time, and reputation.
Why is it so hard to make smart business decisions?
Businesses are complex systems, and they have many moving parts. It is difficult for people in charge of businesses to manage multiple priorities simultaneously and also deal with uncertainty.
The key to making good decisions is to understand how these factors affect the system as a whole.
You must first consider what each piece of the system does and why. Next, consider how each piece interacts with the others.
Ask yourself if there are hidden assumptions that have influenced your behavior. If so, it might be worth reexamining them.
You can always ask someone for help if you still have questions after all of this. They might see things differently than you and may have some insights that could help find a solution.
Statistics
- The profession is expected to grow 7% by 2028, a bit faster than the national average. (wgu.edu)
- The average salary for financial advisors in 2021 is around $60,000 per year, with the top 10% of the profession making more than $111,000 per year. (wgu.edu)
- Our program is 100% engineered for your success. (online.uc.edu)
- UpCounsel accepts only the top 5 percent of lawyers on its site. (upcounsel.com)
- As of 2020, personal bankers or tellers make an average of $32,620 per year, according to the BLS. (wgu.edu)
External Links
How To
How does Lean Manufacturing work?
Lean Manufacturing techniques are used to reduce waste while increasing efficiency by using structured methods. They were developed by Toyota Motor Corporation in Japan during the 1980s. The aim was to produce better quality products at lower costs. Lean manufacturing emphasizes removing unnecessary steps from the production process. It is made up of five elements: continuous improvement, continuous improvement, just in-time, continuous change, and 5S. The production of only what the customer needs without extra work is called pull systems. Continuous improvement is the continuous improvement of existing processes. Just-in-time refers to when components and materials are delivered directly to the point where they are needed. Kaizen is continuous improvement. This can be achieved by making small, incremental changes every day. Fifth, the 5S stand for sort, set up in order to shine, standardize, maintain, and standardize. These five elements are used together to ensure the best possible results.
The Lean Production System
Six key concepts are the basis of lean production:
-
Flow is about moving material and information as near as customers can.
-
Value stream mapping - break down each stage of a process into discrete tasks and create a flowchart of the entire process;
-
Five S's: Sort, Shine Standardize, Sustain, Set In Order, Shine and Shine
-
Kanban - visual cues such as stickers or colored tape can be used to track inventory.
-
Theory of Constraints - Identify bottlenecks in the process, and eliminate them using lean tools such kanban boards.
-
Just-in-time - deliver components and materials directly to the point of use;
-
Continuous improvement - make incremental improvements to the process rather than overhauling it all at once.