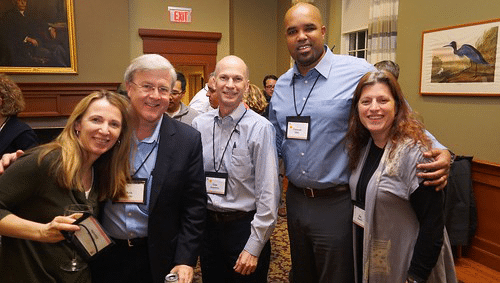
A supply chain decision making framework is a process that will help companies make decisions about different aspects of their business. Communication is a key component. The five steps that make up the rational process are: identifying the problem; analyzing potential solutions; gathering data; analyzing possible outcomes; deciding on the best solution.
Supply chain drivers include inventory.
One of the most important functions of manufacturing companies is managing inventory. This allows the production of the right product at just the right time and place. This function is more important in a global market where products can be manufactured anywhere. It plays an important part in a company’s efficiency and responsiveness.
The ability to anticipate customer requirements and adapt to changing circumstances is key to inventory management. Information about production schedules, inventory levels and other relevant information must be shared by companies with their partners. This allows them quickly respond to market changes. This dynamic market requires inventory management to make sure companies are able to meet customer demands.
Collaboration and communication is key
Communication and collaboration are vital in today's fast-paced business world. These relationships can help companies increase their ability to meet new market demands and differentiate themselves. Collaboration can help companies gain access to new resources, improve their skills, and stay competitive. It can also help businesses expand their customer base.
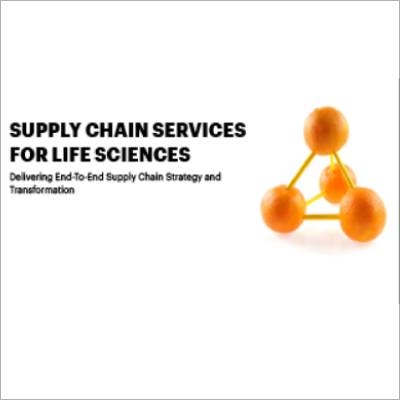
Creating successful collaborative relationships requires high levels of commitment and trust. Organisations must also have a culture that supports collaboration.
Financial attributes
Supply chain decision making should not be limited to economic factors. It should consider financial and other environmental factors when deciding on supply chain decisions. It is essential that cash flows in the supply chains are improved. These attributes will affect the level and quality of working capital both at suppliers and buyers. This is important because the cash flow level is directly related to the level of finance leverage, access to capital, and financial stability of suppliers. SCF is improved through financial attributes. Additionally, they play an important role when it comes to investment in green technologies and policy. Additionally, environmental and financial policies are directly related to social values.
The framework proposed provides a framework for decision-making in the supply chain and interlinks all components. It also identifies open research questions. This framework can be used across all industries and sectors.
Environment attributes
Incorporating environmental attributes into the supply chain decision making framework is a growing trend, driven by a growing awareness of environmental concerns. Companies often adopt environmental performance measurements for a variety of reasons, including to identify potential opportunities for improvement and achieve better co-operation with suppliers. While environmental performance measurement can be a complex issue, it is important to remember that the benefits to both parties can be substantial.
These are financial, environmental, and social criteria. The framework should help enterprises select the most environmentally-friendly suppliers for their business. It should also assist them in adopting environmental practices within their companies.
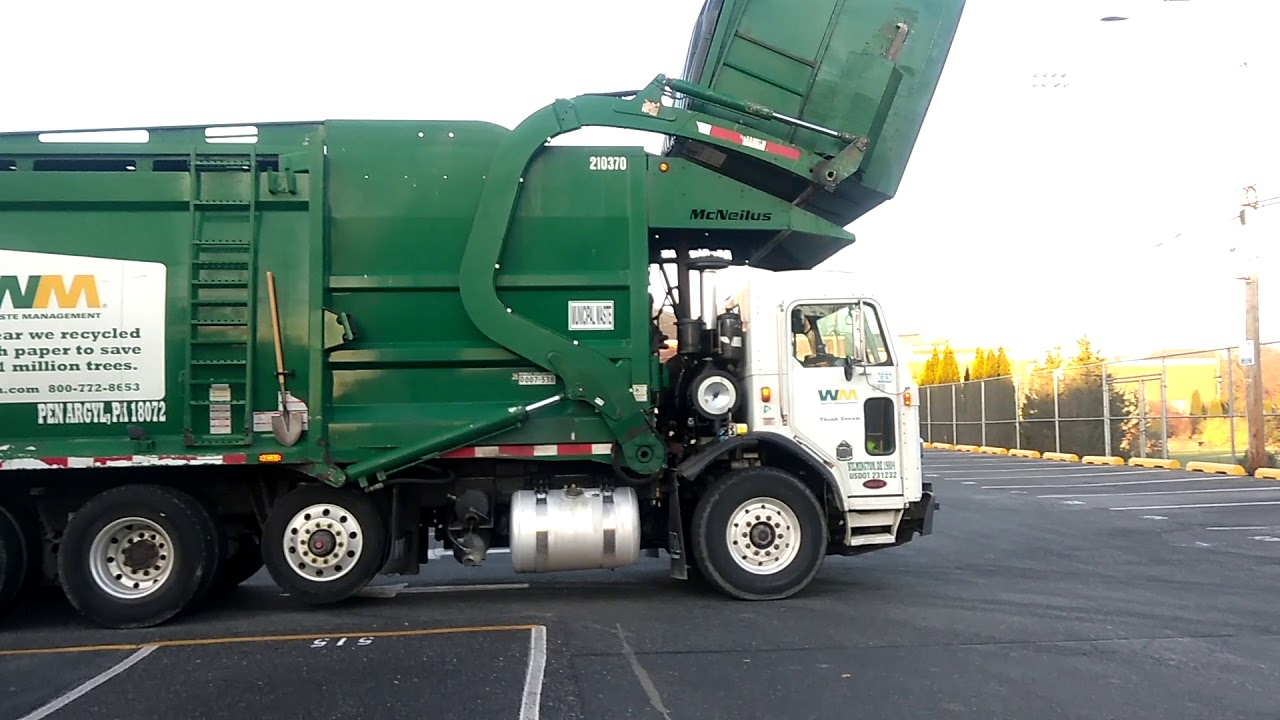
Prioritizing
Supply chain decision making involves the importance of prioritizing demand. It is vital to identify and allocate resources for the highest-profitable demand. This may require delaying orders or offering a replacement product. This will help to manage risk. The entire process should be documented and communicated with all levels of management. While the supply side should input costs, the demand side should have more information about customers' needs and goals.
Next, you need to find opportunities to acquire capacity, raw materials, or labor pools. One option for a company is to look into alternative sources of raw materials at lower prices and with shorter lead times. However, this can impact margins and working capital. It may also be necessary to expand operations outside of peak hours or to obtain additional transportation capacity.
FAQ
How does Six Sigma work
Six Sigma employs statistical analysis to identify problems, measure them and analyze root causes. Six Sigma also uses experience to correct problems.
The first step is identifying the problem.
The data is then analyzed and collected to identify trends.
Then, corrective actions can be taken to resolve the problem.
The data are then reanalyzed to see if the problem is solved.
This cycle will continue until the problem is solved.
What is the difference between TQM and Six Sigma?
The key difference between the two quality management tools is that while six-sigma focuses its efforts on eliminating defects, total quality management (TQM), focuses more on improving processes and reducing cost.
Six Sigma is a method for continuous improvement. It emphasizes the elimination and improvement of defects using statistical methods, such as control charts, P-charts and Pareto analysis.
The goal of this method is to reduce variation in product output. This is done by identifying and correcting the root causes of problems.
Total Quality Management involves monitoring and measuring every aspect of the organization. This includes training employees to improve their performance.
It is used to increase productivity.
What role can a manager fill in a company’s management?
Different industries have different roles for managers.
A manager is generally responsible for overseeing the day to day operations of a company.
He/she is responsible for ensuring that the company meets all its financial obligations and produces the goods or services customers want.
He/she will ensure that employees follow all rules and regulations, and adhere to quality standards.
He/she oversees marketing campaigns and plans new products.
Six Sigma is so popular.
Six Sigma is easy to implement and can produce significant results. It provides a framework that allows for improvement and helps companies concentrate on what really matters.
What are the five management methods?
The five stages of a business include planning, execution (monitoring), review, evaluation, and review.
Setting goals for the future is part of planning. It includes defining what you want to achieve and how you plan to do it.
Execution occurs when you actually carry out the plans. You need to make sure they're followed by everyone involved.
Monitoring is a way to track progress towards your objectives. Regular reviews of performance against budgets and targets should be part of this process.
Review events take place at each year's end. They give you an opportunity to review the year and assess how it went. If not, then it may be possible to make adjustments in order to improve performance next time.
Following the annual review, evaluation is done. It helps to determine what worked and what didn’t. It also provides feedback on the performance of people.
Statistics
- Hire the top business lawyers and save up to 60% on legal fees (upcounsel.com)
- Our program is 100% engineered for your success. (online.uc.edu)
- This field is expected to grow about 7% by 2028, a bit faster than the national average for job growth. (wgu.edu)
- The average salary for financial advisors in 2021 is around $60,000 per year, with the top 10% of the profession making more than $111,000 per year. (wgu.edu)
- As of 2020, personal bankers or tellers make an average of $32,620 per year, according to the BLS. (wgu.edu)
External Links
How To
How does Lean Manufacturing work?
Lean Manufacturing methods are used to reduce waste through structured processes. These processes were created by Toyota Motor Corporation, Japan in the 1980s. The primary goal was to make products with lower costs and maintain high quality. Lean manufacturing eliminates unnecessary steps and activities from a production process. It is composed of five fundamental elements: continuous improvement; pull systems, continuous improvements, just-in–time, kaizen, continuous change, and 5S. The production of only what the customer needs without extra work is called pull systems. Continuous improvement is the continuous improvement of existing processes. Just-in time refers to components and materials being delivered right at the place they are needed. Kaizen refers to continuous improvement. It is achieved through small changes that are made continuously. Fifth, the 5S stand for sort, set up in order to shine, standardize, maintain, and standardize. These five elements can be combined to achieve the best possible results.
The Lean Production System
The lean production system is based on six key concepts:
-
Flow - The focus is on moving information and material as close as possible to customers.
-
Value stream mapping is the ability to divide a process into smaller tasks, and then create a flowchart that shows the entire process.
-
Five S's: Sort, Shine Standardize, Sustain, Set In Order, Shine and Shine
-
Kanban - use visual signals such as colored tape, stickers, or other visual cues to keep track of inventory;
-
Theory of constraints: Identify bottlenecks and use lean tools such as kanban boards to eliminate them.
-
Just-in-time delivery - Deliver components and materials right to your point of use.
-
Continuous improvement - incremental improvements are made to the process, not a complete overhaul.