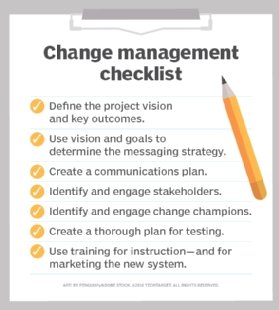
Last mile logistics become more complicated as consumers increasingly depend on online channels to fulfill their needs. This article discusses last mile logistics and the advantages of third-party logistics companies. You'll find out how to improve your last mile delivery while maintaining operational excellence. Learn about new technologies, and how to leverage them to your benefit.
Logistics last mile challenges
Last mile logistics can be difficult for rural areas. The distance between urban and rural delivery points can be several miles, and traffic congestion can slow deliveries. With the rise of ecommerce, it is more important than ever to deliver faster and have free delivery. This means that logistics companies need to improve delivery and fulfillment to meet customer demands.
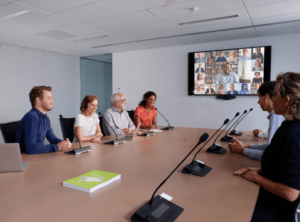
Last mile distribution is unpredictable and can lead to long journeys or insufficient transportation. These factors can result in increased costs and longer delays. Companies should prepare for unanticipated events. If a driver is ill or unable deliver the product on schedule, operators must immediately dispatch a substitute driver.
Even though last-mile logistics is difficult, there are new technologies that can make delivery quicker and more efficient. Route optimization technology can help you save both time and money by identifying the most efficient routes. Advanced machine-learning systems analyze road conditions, weather patterns, and traffic congestion to determine the best route. Drivers can use advanced software to manage their routes and avoid colliding.
Benefits of third party logistics providers
Businesses have a variety of benefits from third-party logistics companies. They can adjust inventory to meet customer demand, reduce overhead when there's less demand, or expand into new markets at the right time. This helps businesses expand into new markets and improve their service. They can also benefit from a much more reliable and consistent supply chain, which is often less expensive than managing their own logistics.
Outsourcing logistics is a great alternative because it allows the company to focus on its core business. It reduces the stress associated with non-core logistics. A third-party logistics provider can also create customized shipping labels or packaging for special orders. These services do come at a charge, so make sure to plan ahead. You can protect yourself against any shipping mishaps with this insurance.
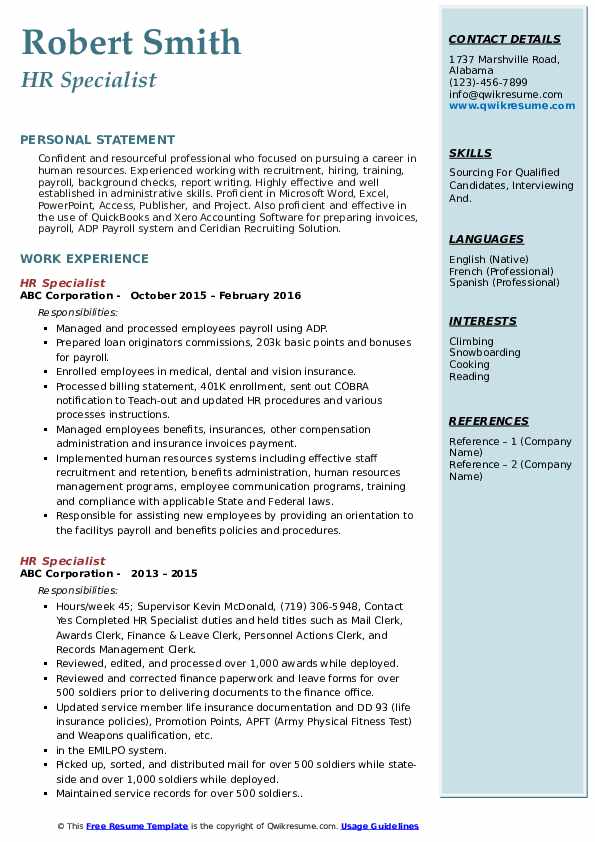
Third-party logistics suppliers also offer warehouse space, inventory administration, and logistics tech to eCommerce businesses. These providers can also deliver goods quickly to customers, which is a huge benefit for eCommerce companies that are growing. An outside logistics provider will take care of stock management, replenishing stock when required. Additionally, they can update inventory when a customer returns an item.
FAQ
What is the main difference between Six Sigma Six Sigma TQM and Six Sigma Six Sigma?
The main difference in these two quality management tools lies in the fact that six sigma is focused on eliminating defects and total quality management (TQM), emphasizes improving processes and reducing costs.
Six Sigma is a methodology for continuous improvement. It emphasizes the elimination and improvement of defects using statistical methods, such as control charts, P-charts and Pareto analysis.
The goal of this method is to reduce variation in product output. This is done by identifying root causes and rectifying them.
Total Quality Management involves monitoring and measuring every aspect of the organization. It also involves training employees to improve performance.
It is often used as a strategy to increase productivity.
Six Sigma is so popular.
Six Sigma is simple to implement and can yield significant results. Six Sigma also gives companies a framework for measuring improvement and helps them focus on what is most important.
Why is project management important for companies?
Project management techniques ensure that projects run smoothly while meeting deadlines.
This is because many businesses depend heavily upon project work to produce products and services.
Companies must manage these projects effectively and efficiently.
Without effective project management, companies may lose money, time, and reputation.
What can a manager do to improve his/her management skillset?
Good management skills are essential for success.
Managers must constantly monitor the performance of their subordinates.
It is important to take immediate action if your subordinate doesn't perform as expected.
It is essential to know what areas need to be improved and how to do it.
What role does a manager play in a company?
The role of a manager varies from one industry to another.
The manager oversees the day-to-day activities of a company.
He/she makes sure that the company meets its financial obligations, and that it produces goods or services that customers desire.
He/she ensures employees adhere to all regulations and quality standards.
He/she oversees marketing campaigns and plans new products.
Statistics
- UpCounsel accepts only the top 5 percent of lawyers on its site. (upcounsel.com)
- The profession is expected to grow 7% by 2028, a bit faster than the national average. (wgu.edu)
- This field is expected to grow about 7% by 2028, a bit faster than the national average for job growth. (wgu.edu)
- Your choice in Step 5 may very likely be the same or similar to the alternative you placed at the top of your list at the end of Step 4. (umassd.edu)
- The average salary for financial advisors in 2021 is around $60,000 per year, with the top 10% of the profession making more than $111,000 per year. (wgu.edu)
External Links
How To
What is Lean Manufacturing?
Lean Manufacturing methods are used to reduce waste through structured processes. These processes were created by Toyota Motor Corporation, Japan in the 1980s. The goal was to produce quality products at lower cost. Lean manufacturing eliminates unnecessary steps and activities from a production process. It consists of five basic elements: pull systems, continuous improvement, just-in-time, kaizen (continuous change), and 5S. Pull systems are able to produce exactly what the customer requires without extra work. Continuous improvement means continuously improving on existing processes. Just-in–time refers when components or materials are delivered immediately to their intended destination. Kaizen refers to continuous improvement. It is achieved through small changes that are made continuously. The 5S acronym stands for sort in order, shine standardize and maintain. To achieve the best results, these five elements must be used together.
Lean Production System
Six key concepts make up the lean manufacturing system.
-
Flow: The goal is to move material and information as close as possible from customers.
-
Value stream mapping- This allows you to break down each step of a process and create a flowchart detailing the entire process.
-
Five S's, Sort, Set in Order, Shine. Standardize. and Sustain.
-
Kanban - use visual signals such as colored tape, stickers, or other visual cues to keep track of inventory;
-
Theory of constraints - identify bottlenecks in the process and eliminate them using lean tools like kanban boards;
-
Just-in-time - deliver components and materials directly to the point of use;
-
Continuous improvement - make incremental improvements to the process rather than overhauling it all at once.