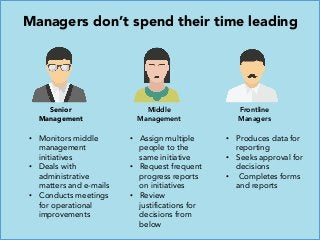
An essential part of project management is the identification and tracking of issues. It allows you keep track of all the details and also keeps everyone informed about how the project progresses. You can use a spreadsheet, a log or any other tool to track issues.
A variety of factors can create problems such as staff shortages or technical failures. They can be high or low priority, and affect a project's success or failure. If ignored, they can cause major problems. These issues can be managed using issue management techniques.
To manage problems, you need a strategy and a plan. You may decide to try multiple avenues of action simultaneously. It is possible to set up an issue tracking dashboard that will keep everyone up to date on the status. You should be careful not misunderstand issues as risks. It is crucial to know the difference.
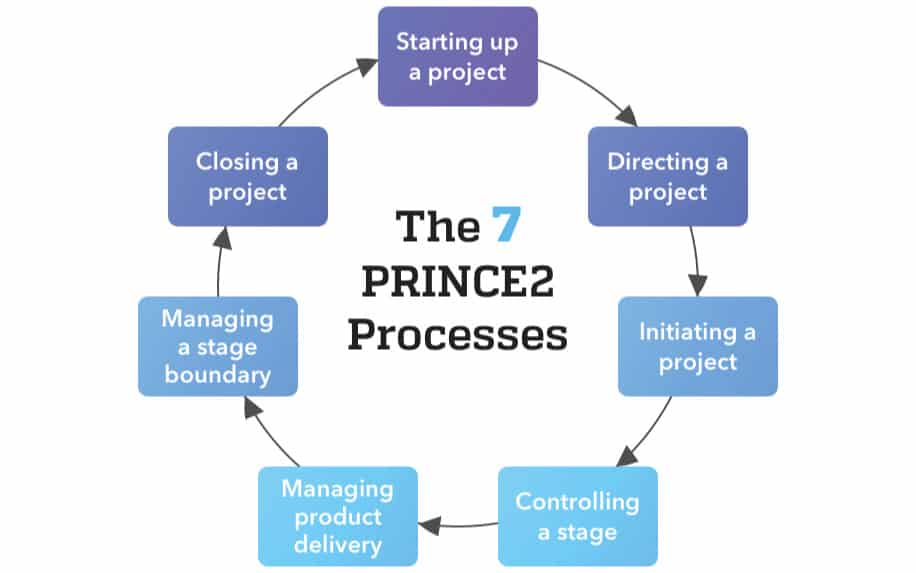
Any level of an organization can have problems. A team may lose a skilled member. You might need to find another resource. Problems can also make it difficult to start a new phase, or achieve the project's goals. Unresolved issues can cause the project to fail. However, effective issue management will help to identify and address the problem while minimizing disruptions.
It is possible to identify issues at all levels. But you must ensure that the information is made available to those who need it. This includes all people involved in reporting on the issue. You might want to use a simple spreadsheet to track issues on projects that are not as complicated as other projects.
Identifying issues is the first step to preventing them. Sometimes, it is easy to identify problems by looking at the smallest details. You might notice that a staff member has been in hospital for more than two weeks. It is important to follow up any issue you have identified in your issue tracker. You can also use it as an archival tool for later use.
You can also find opportunities in the face of problems. If a member of your team is suffering from a medical emergency, it may be possible to hire another member. The issue may also offer a chance to solve a more complex problem. You can identify potential risks before they become problems.
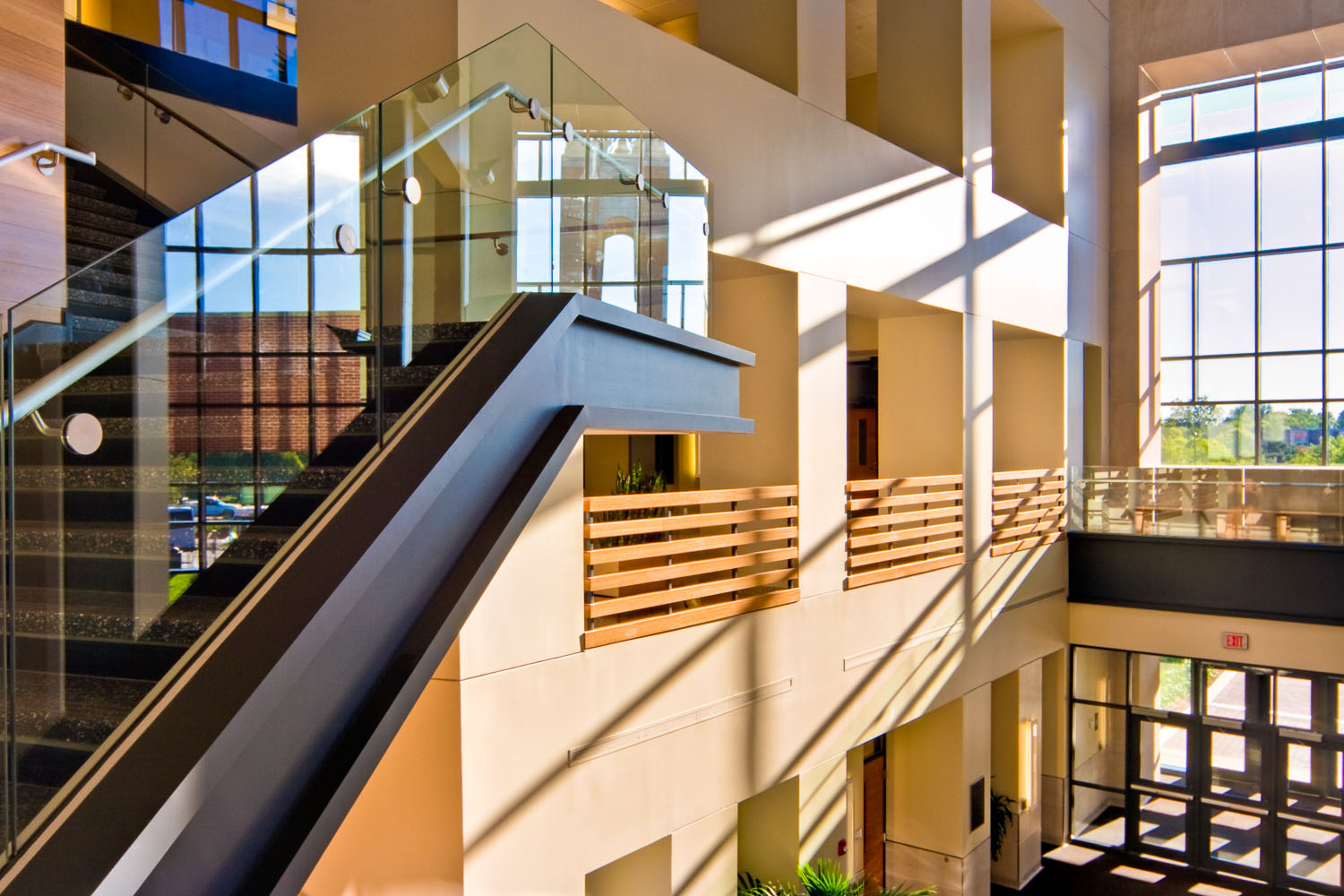
Issue management is also known as information technology service or project management. Whatever the title, issue management is crucial to the success of any project. This involves tracking and identifying issues, assessing their impact, and creating a plan to address them. It is essential to ensure that the process is connected to project governance.
An issue log, spreadsheet, or other project management tool can help you track your issues. In general, it is important to keep the issue log current with status reports as well as resolution comments and actions. Assign members of your team to the issues if you are able. It should also contain a detailed plan to resolve the issue.
FAQ
What are the steps in the decision-making process in management?
Managers are faced with complex and multifaceted decisions. It involves many factors, including but not limited to analysis, strategy, planning, implementation, measurement, evaluation, feedback, etc.
Management of people requires that you remember that they are just as human as you are, and can make mistakes. You are always capable of improving yourself, and there's always room for improvement.
This video will explain how decision-making works in Management. We discuss the different types of decisions and why they are important, every manager should know how to navigate them. You'll learn about the following topics:
Why is project management important for companies?
To ensure projects run smoothly and meet deadlines, project management techniques are employed.
This is because most businesses rely on project work for their products and services.
Companies must manage these projects effectively and efficiently.
Companies that do not manage their projects effectively risk losing time, money, or reputation.
Six Sigma is so well-known.
Six Sigma is easy to use and can lead to significant improvements. Six Sigma also gives companies a framework for measuring improvement and helps them focus on what is most important.
Statistics
- The profession is expected to grow 7% by 2028, a bit faster than the national average. (wgu.edu)
- Our program is 100% engineered for your success. (online.uc.edu)
- Your choice in Step 5 may very likely be the same or similar to the alternative you placed at the top of your list at the end of Step 4. (umassd.edu)
- The BLS says that financial services jobs like banking are expected to grow 4% by 2030, about as fast as the national average. (wgu.edu)
- This field is expected to grow about 7% by 2028, a bit faster than the national average for job growth. (wgu.edu)
External Links
How To
How can you use the Kaizen method?
Kaizen means continuous improvement. Kaizen is a Japanese concept that encourages constant improvement by small incremental changes. It's a process where people work together to improve their processes continuously.
Kaizen, a Lean Manufacturing method, is one of its most powerful. This concept requires employees to identify and solve problems during manufacturing before they become major issues. This increases the quality of products and reduces the cost.
Kaizen is the idea that every worker should be aware of what is going on around them. Correct any errors immediately to avoid future problems. Report any problem you see at work to your manager.
There are some basic principles that we follow when doing kaizen. When working with kaizen, we always start with the end result and move towards the beginning. We can improve the factory by first fixing the machines that make it. Then, we fix the machines that produce components and then the ones that produce raw materials. Then, we fix those who work directly with the machines.
This approach is called 'kaizen' because it focuses on improving everything steps by step. We finish fixing the factory and then go back to the beginning. This continues until we achieve perfection.
You need to know how to measure the effectiveness of kaizen within your business. There are several ways that you can tell if your kaizen system is working. Another method is to see how many defects are found on the products. Another way is to check how much productivity has grown since kaizen was implemented.
To determine if kaizen is effective, you should ask yourself why you chose to implement kaizen. Is it because the law required it or because you want to save money. Did you really believe that it would be a success factor?
If you answered yes to any one of these questions, congratulations! You are now ready to begin kaizen.