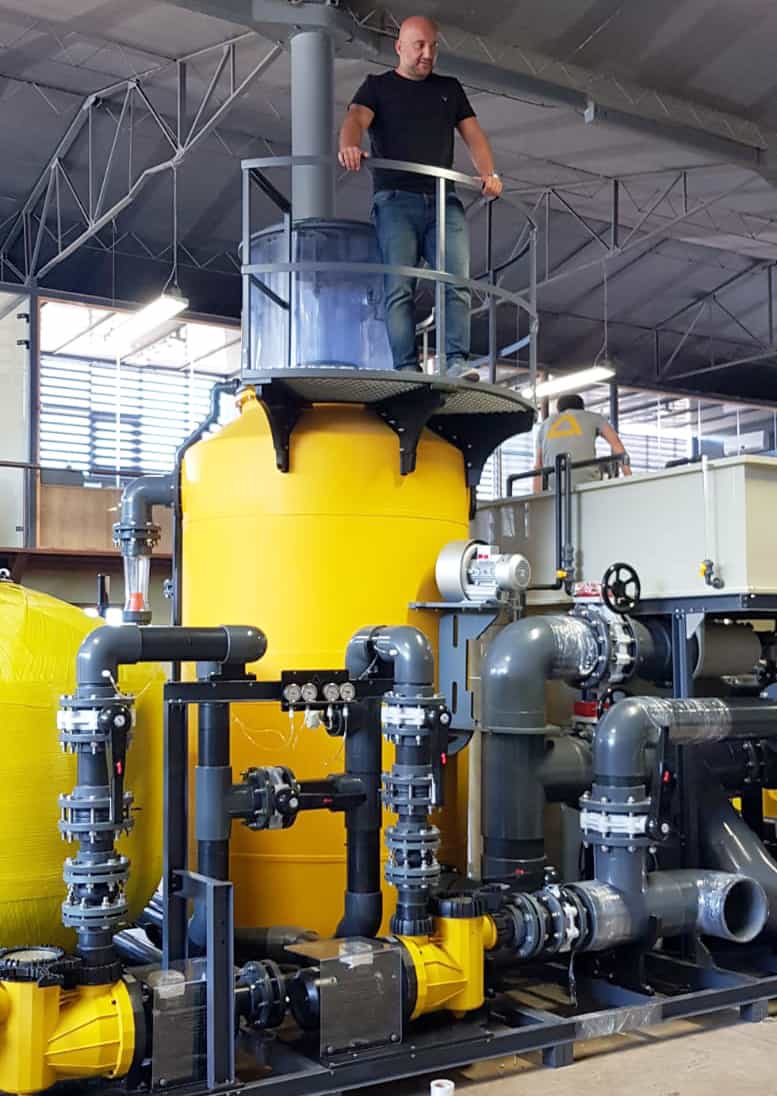
Before you can begin working on a project you will need to create a project management plan. This document will define the process for obtaining resources, developing the resource management plan, and assigning roles for everyone. Your team will also need to be involved in the discussion. To ensure your project's delivery on time and within budget you must involve all your stakeholders. Once you have your plan in writing, you will want to discuss it your team.
Designing a project plan
Before creating a detailed project management plan, it's important to conduct some basic assessments. This includes determining the expected project outcome as well as the due date. It is also important for weekly commitments to be determined. Developing a project management plan will reduce the errors and time spent on the project. In addition, this document will outline how the project will be delivered. Once these initial steps are completed the project manager can proceed with the creation of a project management plan.
The project scope statement is an integral part of the project management plan. To avoid any confusion in the future, it is vital to define the project's scope. In addition, it is critical to identify any possible resources that may be needed for the project. The document should also contain strategies for minimizing risks. It is important to include all deliverables and deadlines. It is crucial to include costs and the required resources.
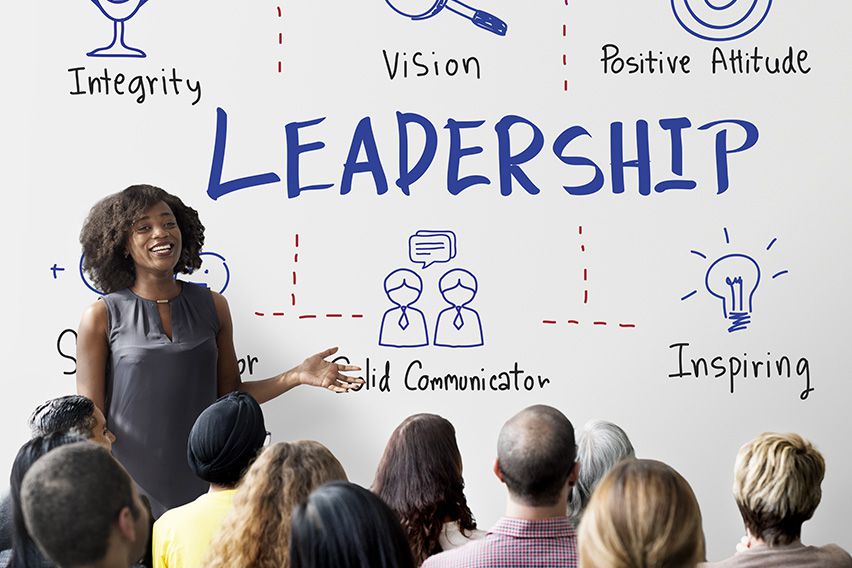
Identifying stakeholders
An important step in developing a project management program is to identify and communicate with stakeholders. Stakeholders refer to individuals that are affected by a particular project. The project manager will need to identify the appropriate focus for each stakeholder. They can include sponsors, customers, employees, management and government officials. Each stakeholder can exert influence over the project deliverables. These are some helpful methods to identify stakeholders:
First, identify all individuals and organizations who are interested in the project. The second step in identifying stakeholders is to assess and determine each stakeholder’s influence and involvement. Stakeholders are best identified early in the project, before the project begins. Once identified, they can then be categorized according to their influence/interest. This assessment should take place throughout the project's lifespan.
A cost estimate is created
Developing a cost estimation is an important step in any project management plan. It serves as a basis for allocating resources and provides a base for project costs. A detailed description of the work required to create a cost estimate. The American Association of Cost Engineers defines cost engineering as an area of engineering practice involving the application of scientific principles and techniques to identify and estimate costs.
An accurate cost estimate must take into account the best available information and the experience of all those involved in the project. Cost estimations must be transparent and open. It is important to refine the cost estimate using technical advice and engineering judgment. It should incorporate data from all parties, including customers. The cost estimate should be accurate and reflect the project's scope.
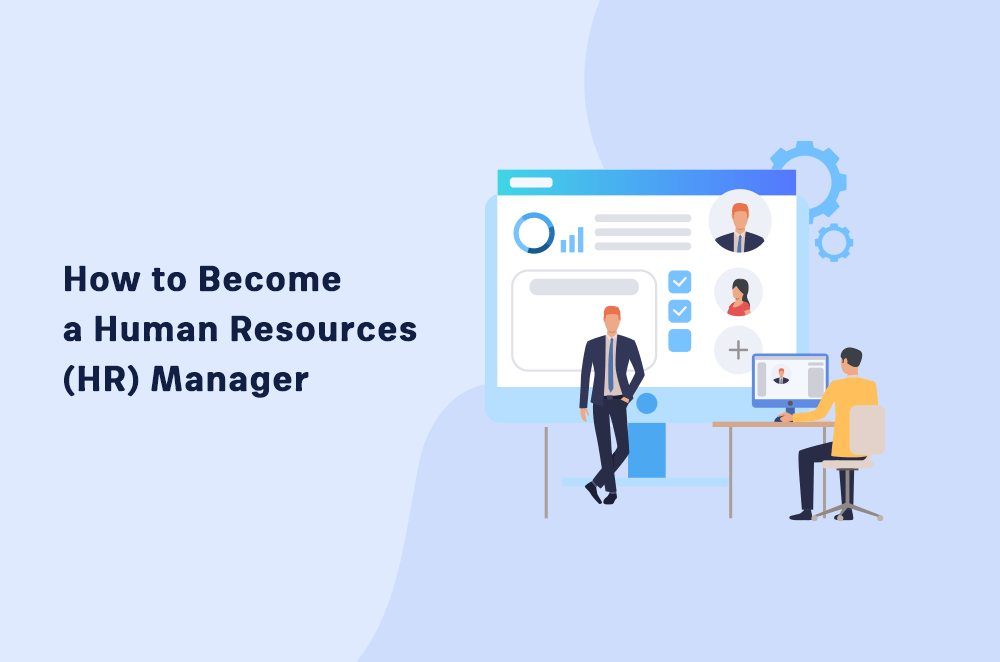
Discussing the plan and your team
Discussing the project management plan with your team is one of the most important steps in creating it. This will ensure everyone in your team is clear about the project plan and what they are expected to do. This plan should list tasks and assign team members. Clear directions and documentation are required to assign tasks. Before you begin the project, make sure everyone understands it. For any questions on the project management plan, you can always reach out.
When discussing the project management plan with your team, be sure to make it as complete as possible. Don't forget to include everyone's input. This plan is not intended to be a final product, but a starting point. Your team and the client should give feedback. This will enable you to make any necessary adjustments to the plan.
FAQ
What are the 5 management processes?
The five stages of any business are planning, execution, monitoring, review, and evaluation.
Setting goals for the future requires planning. This includes setting goals for the future and defining what you want.
Execution occurs when you actually carry out the plans. They must be followed by all parties.
Monitoring is the process of evaluating your progress toward achieving your objectives. Monitoring should include regular reviews of performance against goals and budgets.
At the end of every year, reviews take place. They provide an opportunity to assess whether everything went well during the year. If not, then it may be possible to make adjustments in order to improve performance next time.
After the annual review is complete, evaluations are conducted. It helps to determine what worked and what didn’t. It also gives feedback on how well people did.
What is the meaning of "project management?"
It refers to the management of activities related to a project.
We help you define the scope of your project, identify the requirements, prepare the budget, organize the team, plan the work, monitor progress and evaluate the results before closing down the project.
How do you manage your employees effectively?
Achieving employee happiness and productivity is key to managing them effectively.
It means setting clear expectations for them and keeping an eye on their performance.
Managers need clear goals to be able to accomplish this.
They should communicate clearly with employees. They also need to make sure that they discipline and reward the best performers.
They must also keep records of team activities. These include:
-
What did we accomplish?
-
How much work was put in?
-
Who did it?
-
What was the moment it was completed?
-
Why was it done?
This information is useful for monitoring performance and evaluating the results.
What is Six Sigma, exactly?
It's a method for quality improvement that focuses on customer service as well as continuous learning. The objective is to eliminate all defects through statistical methods.
Motorola invented Six Sigma in 1986 as part its efforts to improve manufacturing.
It was quickly adopted by the industry and many companies are now using six-sigma to improve product design, production, delivery, customer service, and product design.
How does Six Sigma work?
Six Sigma employs statistical analysis to identify problems, measure them and analyze root causes. Six Sigma also uses experience to correct problems.
First, identify the problem.
The data is then analyzed and collected to identify trends.
The problem can then be fixed by taking corrective measures.
Finally, data will be reanalyzed to determine if there is an issue.
This cycle will continue until the problem is solved.
What is the difference of a program and project?
A project is temporary; a program is permanent.
A project typically has a defined goal and deadline.
It is usually done by a group that reports back to another person.
A program typically has a set goal and objective.
It is usually done by one person.
Statistics
- The BLS says that financial services jobs like banking are expected to grow 4% by 2030, about as fast as the national average. (wgu.edu)
- Our program is 100% engineered for your success. (online.uc.edu)
- The profession is expected to grow 7% by 2028, a bit faster than the national average. (wgu.edu)
- 100% of the courses are offered online, and no campus visits are required — a big time-saver for you. (online.uc.edu)
- This field is expected to grow about 7% by 2028, a bit faster than the national average for job growth. (wgu.edu)
External Links
How To
How do you do the Kaizen method?
Kaizen means continuous improvement. This Japanese term refers to the Japanese philosophy of continuous improvement that emphasizes incremental improvements and constant improvement. This is a collaborative process in which people work together to improve their processes continually.
Kaizen is one of the most effective methods used in Lean Manufacturing. This concept requires employees to identify and solve problems during manufacturing before they become major issues. This will increase the quality and decrease the cost of the products.
Kaizen is a way to raise awareness about what's happening around you. To prevent problems from happening, any problem should be addressed immediately. Report any problem you see at work to your manager.
There are some basic principles that we follow when doing kaizen. We always start from the end product and move toward the beginning. We can improve the factory by first fixing the machines that make it. Then, we fix the machines that produce components and then the ones that produce raw materials. Finally, we repair the workers who are directly involved with these machines.
This is why it's called "kaizen" because it works step-by-step to improve everything. When we are done fixing the whole factory, we go back to the beginning and continue until we reach perfection.
It is important to understand how to measure the effectiveness and implementation of kaizen in your company. There are several ways to determine whether kaizen is working well. Another method is to see how many defects are found on the products. Another way is to check how much productivity has grown since kaizen was implemented.
Another way to know whether kaizen is working is to ask yourself why did you decide to implement kaizen. It was because of the law, or simply because you wanted to save some money. Did you really think that it would help you achieve success?
If you answered yes to any one of these questions, congratulations! You're ready to start kaizen.