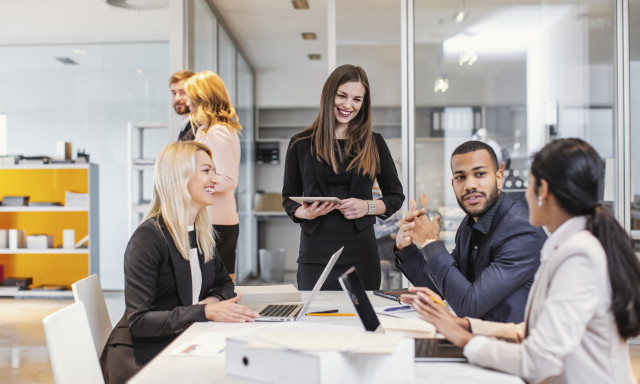
You can get engineering project management training to make sure you are ready to manage your projects. Not only will you have the technical skills and knowledge to do these tasks, but you'll also learn how interact with others to get the job done.
Additionally, you will be able examine a range different methods and tools for managing projects. It will also teach you how to make a detailed work breakdown and cost estimates. Learn how to calculate earned value, create a project plan, and manage issues throughout the project's life cycle.
Project engineers generally have at most three years of experience. Project engineers need to be adept at managing projects and making quick decisions in order to be successful on the job. They also need to be good communicators and have a knack for writing reports that non-engineers can understand. They often have to travel to meet contractors and work on the jobsite. Sometimes they may have to work at the office.
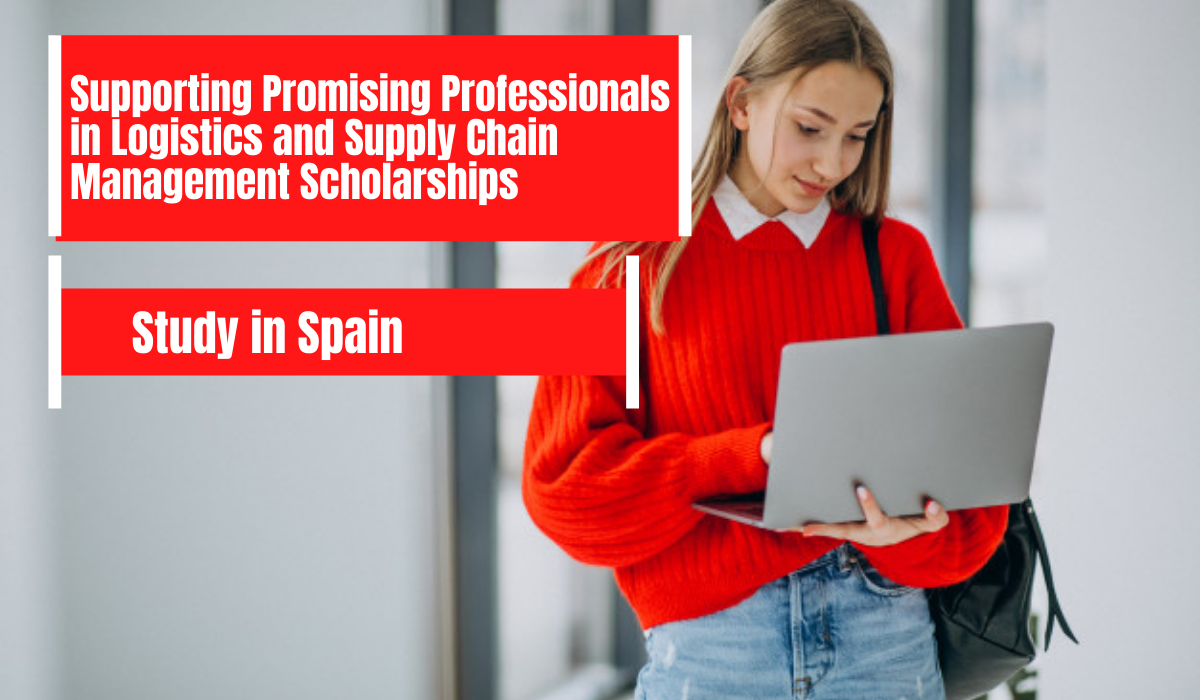
A degree in engineering is one of best ways to be a project manager. Through internships or training courses, you can also acquire the skills and knowledge required to succeed in this area. Regardless of your educational background, you'll have to be willing to put in the time and effort to get the most out of your training.
Project engineering training goes well beyond just traditional scheduling. It also includes practical exercises and hands-on workshops. Real-world case studies are included to provide real-world experience with the information. You will be able practice the skills you have learned and this will allow you success in your engineering career.
Design is one of the most fundamental aspects of project engineering. This allows you to analyze your project's needs and design effective solutions. You will also learn how to use CAD to create precise designs.
It is important to understand how to properly create requirements documents. You'll also want to learn how to create a project plan, including a critical path schedule. This course will allow you to examine a range of cost estimates and calculate earned value. It will also allow you to determine the true cost of quality.
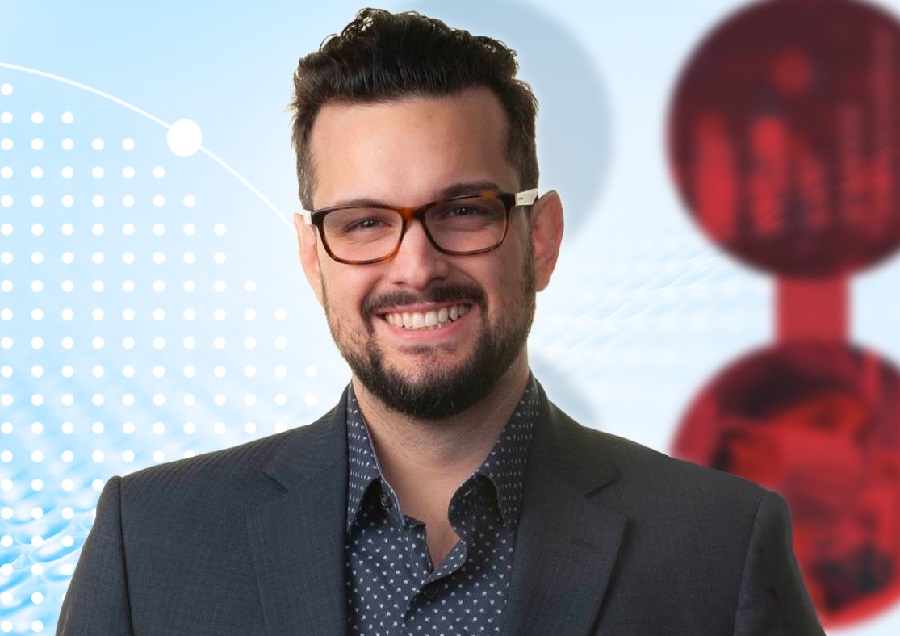
A project engineer must have a solid understanding of math, including trigonometry. Because complex problems can only be solved with a solid foundation in math, this is a must-have skill. It is also important to understand how to calculate the project's net present value, which shows the customer how it will benefit them. You should also consider the business argument for the project. This involves analysing stakeholder expectations and needs, identifying key deliverables, then determining the business model.
Project Management Institute offers the PMP credential. This credential demonstrates knowledge and experience with project management. To obtain this credential you will need to pass a test. Your certification must be maintained for three years.
FAQ
What are the 3 basic management styles?
The three basic management styles are: authoritarian, laissez-faire, and participative. Each style has strengths and flaws. Which style do your prefer? Why?
Autoritarian – The leader sets the direction for everyone and expects them to follow. This style is best when the organization has a large and stable workforce.
Laissez-faire – The leader gives each individual the freedom to make decisions for themselves. This style is best when the organization has a small but dynamic group.
Participative – The leader listens and takes in ideas from all. This style is most effective in smaller organizations, where everyone feels valued.
What is a simple management tool that aids in decision-making and decision making?
A decision matrix, a simple yet powerful tool for managers to make decisions, is the best. It helps them to think strategically about all options.
A decision matrix is a way of representing alternatives as rows and columns. It is easy to see how each option affects the other options.
We have four options in this example. They are represented by the boxes to the left of the matrix. Each box represents an alternative. The top row represents the current state of affairs, and the bottom row is indicative of what would happen in the event that nothing were done.
The effect of selecting Option 1 is shown in the middle column. It would increase sales by $2 million to 3 million in this instance.
The following columns illustrate the impact of Options 2 and 3. These positive changes can increase sales by $1 million or $500,000. These changes can also have negative effects. For instance, Option 2 increases cost by $100 thousand while Option 3 reduces profits by $200 thousand.
The final column shows results of choosing Option 4. This involves decreasing sales by $1 million.
The best part of using a decision-matrix is that it doesn't require you to know which numbers belong where. You can just glance at the cells and see immediately if one given choice is better.
The matrix has already done all of the work. It is as simple as comparing the numbers within the relevant cells.
Here's an example showing how you might use a Decision Matrix in your business.
You need to decide whether to invest in advertising. If you do this, you will be able to increase revenue by $5000 per month. However, additional expenses of $10 000 per month will be incurred.
If you look at the cell that says "Advertising", you can see the number $15,000. Advertising is worth more than its cost.
What are the steps to take in order to make a management decision?
Managers face complex and multifaceted decision-making challenges. It involves many factors, such as analysis and strategy, planning, execution, measurement, evaluation, feedback etc.
When managing people, the most important thing to remember is that they are just human beings like you and make mistakes. As such, there are always opportunities for improvement, especially when you put in the effort to improve yourself.
This video shows you how management makes decisions. We discuss the different types of decisions and why they are important, every manager should know how to navigate them. These topics are covered in this course:
What's the difference between Six Sigma and TQM?
The key difference between the two quality management tools is that while six-sigma focuses its efforts on eliminating defects, total quality management (TQM), focuses more on improving processes and reducing cost.
Six Sigma is a method for continuous improvement. It emphasizes the elimination of defects by using statistical methods such as control charts, p-charts, and Pareto analysis.
This method seeks to decrease variation in product output. This is achieved by identifying and addressing the root causes of problems.
Total quality management is the measurement and monitoring of all aspects within an organization. Training employees is also part of total quality management.
It is frequently used as an approach to increasing productivity.
What are the most common errors made by managers?
Sometimes managers make it harder for their employees than is necessary.
They might not give enough support and delegate the right responsibilities to their staff.
Additionally, many managers lack communication skills that are necessary to motivate and direct their teams.
Managers sometimes set unrealistic expectations of their teams.
Managers may prefer to solve every problem for themselves than to delegate responsibility.
Statistics
- The average salary for financial advisors in 2021 is around $60,000 per year, with the top 10% of the profession making more than $111,000 per year. (wgu.edu)
- UpCounsel accepts only the top 5 percent of lawyers on its site. (upcounsel.com)
- As of 2020, personal bankers or tellers make an average of $32,620 per year, according to the BLS. (wgu.edu)
- Hire the top business lawyers and save up to 60% on legal fees (upcounsel.com)
- The profession is expected to grow 7% by 2028, a bit faster than the national average. (wgu.edu)
External Links
How To
How can Lean Manufacturing be done?
Lean Manufacturing methods are used to reduce waste through structured processes. They were created in Japan by Toyota Motor Corporation during the 1980s. The main goal was to produce products at lower costs while maintaining quality. Lean manufacturing emphasizes removing unnecessary steps from the production process. It is composed of five fundamental elements: continuous improvement; pull systems, continuous improvements, just-in–time, kaizen, continuous change, and 5S. Pull systems allow customers to get exactly what they want without having to do extra work. Continuous improvement is constantly improving upon existing processes. Just-in time refers to components and materials being delivered right at the place they are needed. Kaizen stands for continuous improvement. Kaizen can be described as a process of making small improvements continuously. Five-S stands for sort. It is also the acronym for shine, standardize (standardize), and sustain. These five elements work together to produce the best results.
Lean Production System
Six key concepts underlie the lean production system.
-
Flow is about moving material and information as near as customers can.
-
Value stream mapping is the ability to divide a process into smaller tasks, and then create a flowchart that shows the entire process.
-
Five S's – Sort, Put In Order Shine, Standardize and Sustain
-
Kanban – visual signals like colored tape, stickers or other visual cues are used to keep track inventory.
-
Theory of constraints: Identify bottlenecks and use lean tools such as kanban boards to eliminate them.
-
Just-intime - Order components and materials at your location right on the spot.
-
Continuous improvement - Make incremental improvements rather than overhauling the entire process.