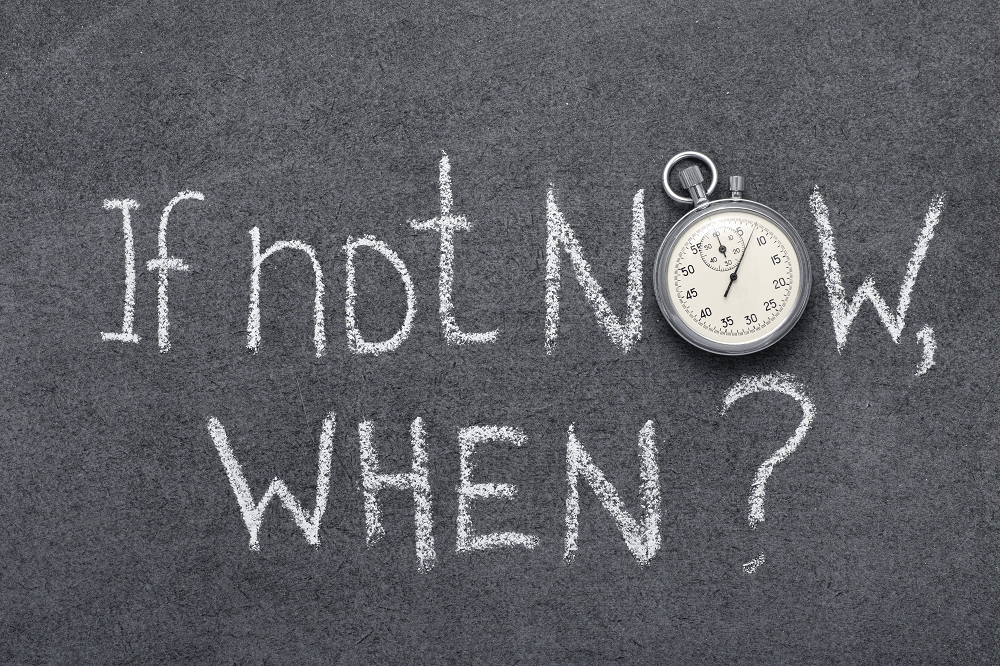
Group factors can have a significant impact on any organisational change. These factors include both the formal and informal members of an organization. While some groups, such as trade unionism, may resist change, the informal group can also be a strong barrier to change. Modifying group dynamics can affect work flows, job design or social organisation and influence systems. Changes can also impact communication patterns and status systems. These factors will need to be understood and dealt with in order for any change to be successful.
Organization resistance to change
Most people's perception of change is what causes resistance to change within organizations. Mullin believes that managers can't do much to fix this problem. There are many ways to address this problem. The two perspectives employees use to approach organisational change are different. Firstly, they form their response to the change by what they see and how they perceive it. Van Tonder's perspective, however, suggests that people create their responses to organisational changes at the individual level.
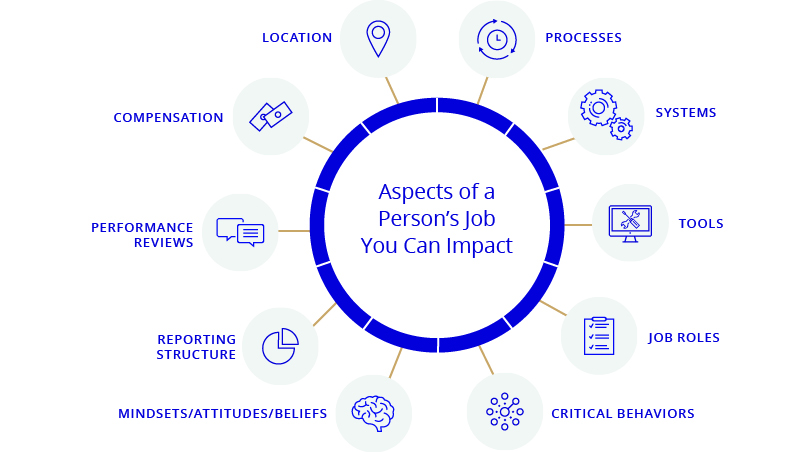
Types of organization change
Organisations experience many types of change. Companies must adapt to keep up with the constantly changing business environment. Adaptive innovation is usually not disruptive. Adaptive change occurs when an organisation strives to improve its processes and strategies. Organisations that undergo transformations should plan for the transition period, and prepare properly. This article will discuss some of the key differences between different types of change and how they can affect an organisation.
External environment has an influence
The external environment has many factors that influence the organisation's performance. These factors do not have a fixed pattern and change at different rates. Instead, they are mutually reinforcing and influence one another. The external environment changes require organizations to adapt and make proactive adjustments. This article will address some of the common factors that can affect external environment change. Understanding the interconnectedness of the external and internal environments is crucial for your organization.
Process-oriented change
Changes that impact workflow, productivity and group cohesion are called process-oriented changes in an organization. Process-oriented change can be seen in robotics in manufacturing plants as well as laser scanning checkout systems at supermarkets. Both types can have a different impact on an organisation's culture. It is important to consider the culture within which your company operates. This article will cover the benefits and differences between process-oriented, and other types or change that may occur within an organization.
Structural changes
Organizational development cannot be completed without change management. While minor changes to policies and tools can have an effect on a business, large-scale changes have the potential to transform a company. The strategy chosen is crucial to the success of such transformations. For a change to be successful, serious planning and preparation are needed. A plan should be developed to achieve the goal. To ensure the success and sustainability of any new strategy, change management should be an ongoing process.
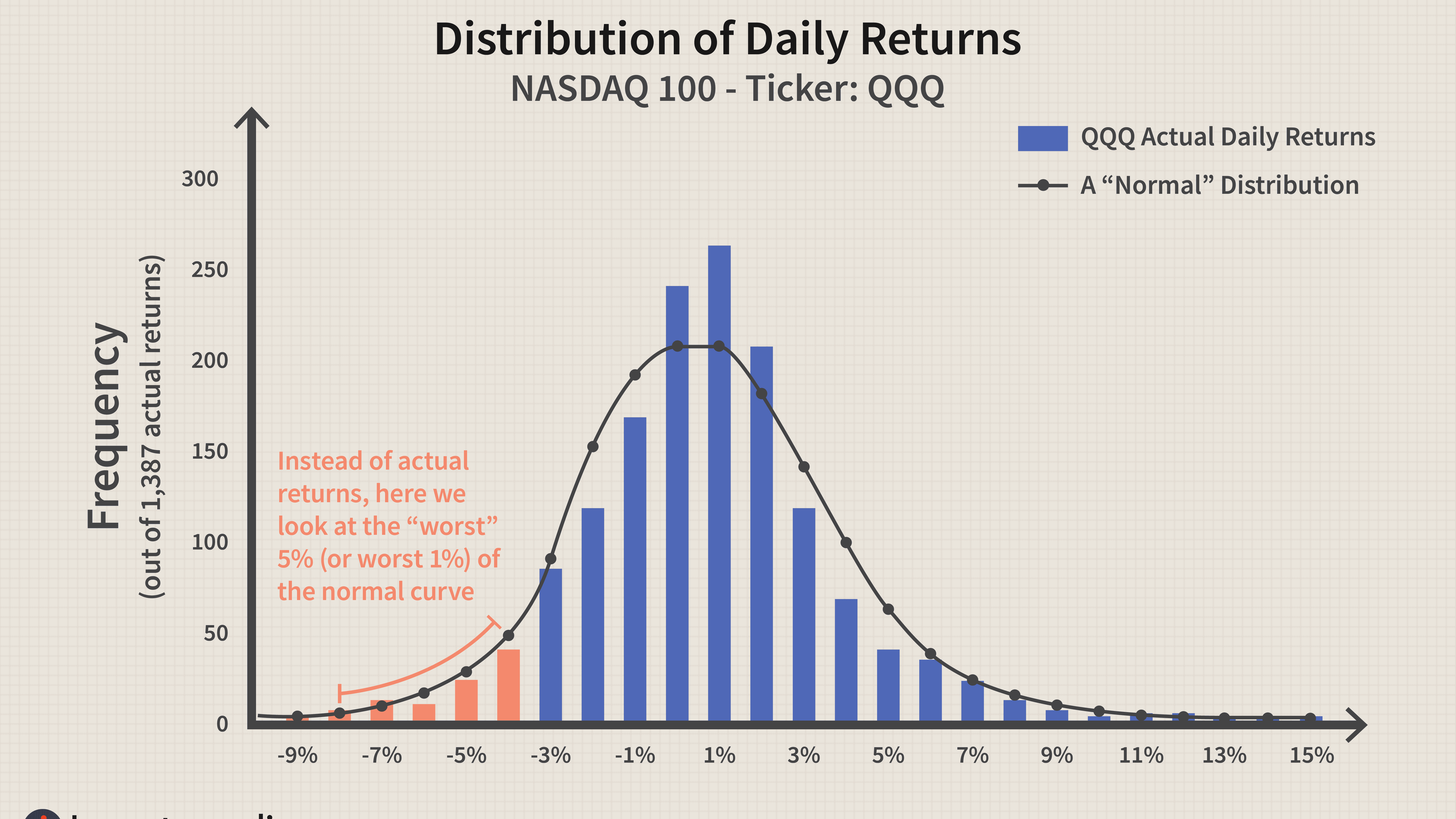
Technological Change
Technology management refers to the process of identifying and implementing new technologies that are beneficial to an organization. The processes and plans involved in technology change management include defining requirements, estimating expected benefits and life spans, determining appropriate sources of technology, and documenting the results. Documenting the process of selecting technologies for an organisation is called a technology management policy and procedure. The process documents all possible solutions and challenges, as well acquisitions of new technology and requests.
FAQ
What do we mean when we say "project management"?
Management is the act of managing activities in order to complete a project.
We help you define the scope of your project, identify the requirements, prepare the budget, organize the team, plan the work, monitor progress and evaluate the results before closing down the project.
What is TQM exactly?
When manufacturing companies realized that price was not enough to compete, the industrial revolution brought about the quality movement. They needed to improve quality and efficiency if they were going to remain competitive.
Management developed Total Quality Management to address the need for improvement. It focused on all aspects of an organisation's performance. It included continuous improvement processes, employee involvement, and customer satisfaction.
What is Six Sigma and how can it help you?
It is a way to improve quality that places emphasis on customer service and continuous learning. It is a method that eliminates defects using statistical techniques.
Motorola's 1986 efforts to improve manufacturing process efficiency led to the creation of Six Sigma.
The idea quickly spread in the industry. Many organizations today use six-sigma methods to improve product design and production, delivery and customer service.
How do you effectively manage employees?
Effectively managing employees requires that you ensure their happiness and productivity.
It means setting clear expectations for them and keeping an eye on their performance.
To do this successfully, managers need to set clear goals for themselves and for their teams.
They should communicate clearly to staff members. They should also ensure that they both reward high performers and discipline those who are not performing to their standards.
They will also need to keep records about their team's activities. These include:
-
What was the result?
-
How much work were you able to accomplish?
-
Who did it?
-
What was the moment it was completed?
-
Why was this done?
This information can help you monitor your performance and to evaluate your results.
What are the four main functions of management?
Management is responsible to plan, organize, direct, and control people and resources. It also includes developing policies and procedures and setting goals.
Management helps an organization achieve its objectives by providing direction, coordination, control, leadership, motivation, supervision, training, and evaluation.
The four main functions of management are:
Planning - Planning is about determining what must be done.
Organizing: Organizing refers to deciding how things should work.
Directing - Directing means getting people to follow instructions.
Controlling – Controlling is the process of ensuring that tasks are completed according to plan.
What is a basic management tool used in decision-making?
A decision matrix is a simple but powerful tool for helping managers make decisions. It helps them to think strategically about all options.
A decision matrix represents alternatives in rows and columns. This allows you to easily see how each choice affects others.
The boxes on the left hand side of this matrix represent four possible choices. Each box represents an option. The top row depicts the current status quo, while the bottom row represents what would happen if no action was taken.
The middle column shows the effect of choosing Option 1. In this example, it would lead to an increase in sales of between $2 million and $3 million.
The effects of options 2 and 3 are shown in the next columns. These are good changes, they increase sales by $1million or $500,000. However, these also involve negative consequences. Option 2, for example, increases the cost by $100 000 while Option 3 decreases profits by $200 000.
The final column shows results of choosing Option 4. This means that sales will decrease by $1 million.
The best thing about using a decision matrix is that you don't need to remember which numbers go where. It's easy to see the cells and instantly know if any one of them is better than another.
The matrix already does all the work. It's as easy as comparing numbers in the appropriate cells.
Here is an example how you might use the decision matrix in your company.
Decide whether you want to invest more in advertising. You'll be able increase your monthly revenue by $5000 if you do. However, this will mean that you'll have additional expenses of $10,000.
You can calculate the net result of investing in advertising by looking at the cell directly below the one that says "Advertising." That number is $15 thousand. Advertising is worth more than its cost.
How do you define Six Sigma?
Six-sigma will be well-known to anyone who has worked in operations research or statistics. Anyone involved in business can benefit.
Because it requires a high level of commitment, only those with strong leadership skills will make an effort necessary to implement it successfully.
Statistics
- Our program is 100% engineered for your success. (online.uc.edu)
- The average salary for financial advisors in 2021 is around $60,000 per year, with the top 10% of the profession making more than $111,000 per year. (wgu.edu)
- 100% of the courses are offered online, and no campus visits are required — a big time-saver for you. (online.uc.edu)
- UpCounsel accepts only the top 5 percent of lawyers on its site. (upcounsel.com)
- Hire the top business lawyers and save up to 60% on legal fees (upcounsel.com)
External Links
How To
How can you use the Kaizen method?
Kaizen means continuous improvement. This Japanese term refers to the Japanese philosophy of continuous improvement that emphasizes incremental improvements and constant improvement. It is a process where people come together to improve their processes.
Kaizen, a Lean Manufacturing method, is one of its most powerful. This concept requires employees to identify and solve problems during manufacturing before they become major issues. This increases the quality of products and reduces the cost.
The main idea behind kaizen is to make every worker aware of what happens around him/her. If something is wrong, it should be corrected immediately so that no problem occurs. So, if someone notices a problem while working, he/she should report it to his/her manager.
There are some basic principles that we follow when doing kaizen. We always start from the end product and move toward the beginning. To improve our factory, for example, we need to fix the machines that produce the final product. Next, we fix the machines which produce components. Then we fix the workers, who directly work with these machines.
This is known as "kaizen", because it emphasizes improving each step. After we're done with the factory, it's time to go back and fix the problem.
It is important to understand how to measure the effectiveness and implementation of kaizen in your company. There are many ways you can determine if kaizen has been implemented well. Another method is to see how many defects are found on the products. Another way to find out how productive your company has been since you implemented kaizen is to measure the increase in productivity.
You can also find out if kaizen works by asking yourself why you decided to implement it. Was it just because it was the law or because you wanted to save money? Did you really think that it would help you achieve success?
If you answered yes to any one of these questions, congratulations! You are ready to start kaizen.