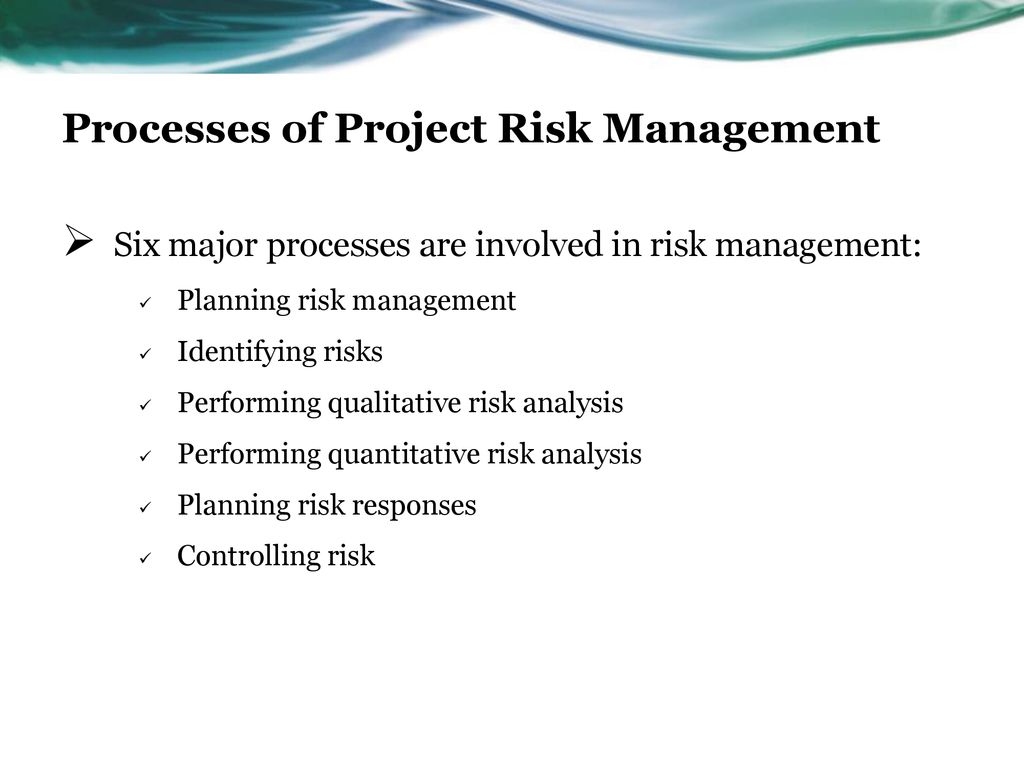
A waste management company is able to assist you when you are looking for a way to dispose of your trash. This service can take care of your trash and provide recycling services. Read on to learn more about the various options for waste management companies, including their costs, environmental impact, and pay-as you-throw payment structures. There are also alternatives to waste management services.
Costs of waste management services
For waste management financing, unit-based pricing is used by municipalities all over the country. Services like transporting waste from landfills to transfer stations are subject to a periodic billing. These fees may range from $1-300 per household per annum. These fees are intended to raise community awareness about the costs of waste management but do not encourage waste reduction. Municipalities may also be eligible for grants from Department of Environmental Protection to cover initial costs.
Although waste management services only make up a small percentage of the municipal tax pie (less than ten%), they can be expensive. Since 2001, Muskoka's share has risen from 7 to 9 percent. For instance, the Township Georgian Bay's cost per tonne has risen almost fourfold. By comparison, costs per tonnage in Muskoka municipalities have fallen nearly by two thirds. However, the cost to transport a tonne is more than twice that of other cities.
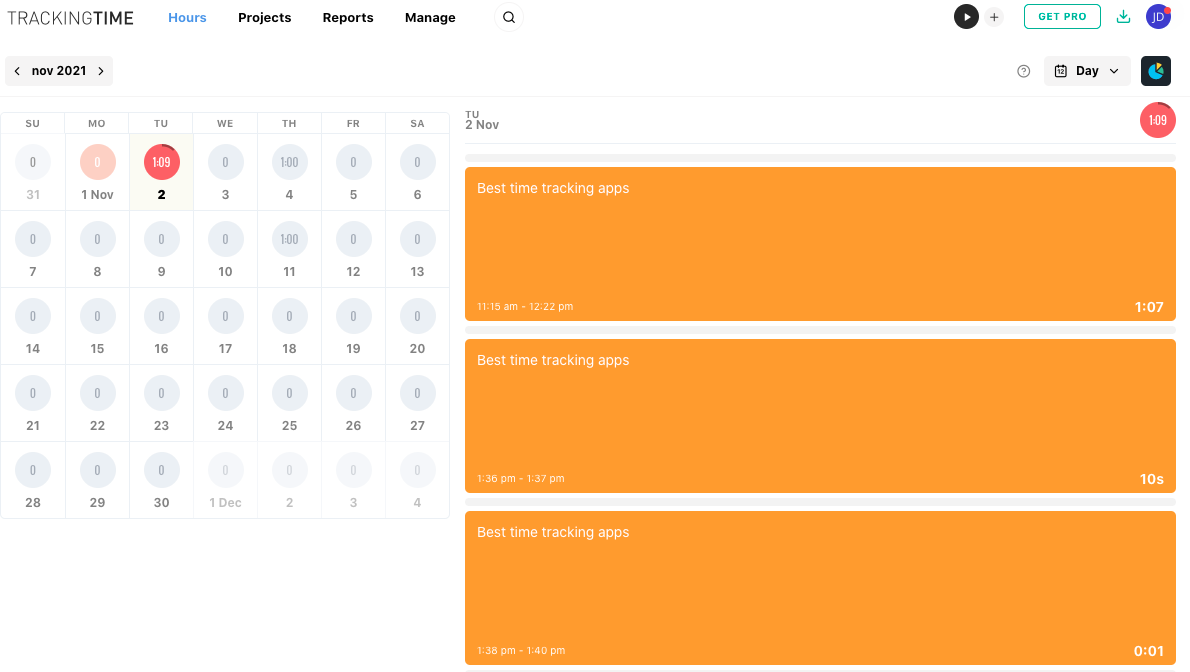
Alternatives to Waste Management Services
Alternative ways of processing waste are needed by the waste management industry. Our civilization produces waste that needs to be processed and disposed of. The problem is that the 20th century invented many things that interfere with the natural recycling cycle. Plastic packaging, oil containers and tires, as well as batteries, electronics, are all examples. Once they have become unusable, the products must be processed and disposed of artificially. Problem is, awareness is slow to change.
Environmental impact of waste management services
The impact of waste management services on the environment is numerous. Among these are the dangers to surface and ground water. Animal and plant life can be affected by trash pollution. Polluted water could pose dangers to animals and humans. Air pollution can also be caused by poor waste management. Air pollution not only causes harm to the environment, but can also lead to breathing problems. Fortunately, there are ways to minimize these impacts.
To reduce the amount of waste generated, cities and landfills must implement policies that target the creation of sustainable waste management. By 2050, there will be 3.4 Gt municipal solid waste in the world. There are laws and policies that can be used to stop the growth of waste in various cities and regions. These measures include integrated technoeconomic mechanisms that create a circular economy and provide effective waste disposal facilities. Import and export control can also be controlled and sustainable products are designed.
Alternatives to the traditional pay-as–you-throw arrangement
Pay-as–you-throw payment models for waste management services offer some advantages and downsides. While some payment arrangements are inequitable and unfair, others encourage waste reduction and are fair. The pay-as you-throw payment system is an effective way of reducing waste and costs while encouraging recycling and composting. In fact, in the United States, more than 7,000 communities now have this type of payment structure.
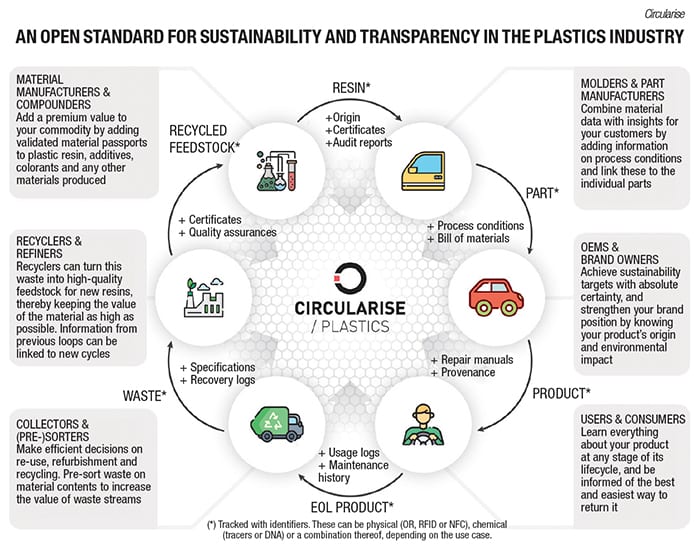
One of the greatest advantages to pay-as–you-throw is that residents are informed about the costs associated with services. Residents are happy to have control over their expenses. Some communities, such as Seekonk, Massachusetts, are phasing in unit-based pricing with flat fees to ease residents into the new system. Residents are now aware of the injustice of charging the same amount to everyone.
FAQ
What is Six Sigma?
Six Sigma uses statistical analysis for problems to be found, measured, analyzed root causes, corrected, and learned from.
The first step in solving a problem is to identify it.
Next, data will be collected and analyzed to determine trends and patterns.
The problem is then rectified.
Final analysis of data is done to determine if the problem has been solved.
This continues until you solve the problem.
How can we create a culture of success in our company?
A positive company culture creates a sense of belonging and respect in its people.
It's based on three main principles:
-
Everybody has something to offer.
-
People are treated with respect
-
There is mutual respect between individuals and groups
These values are reflected by the way people behave. They will show consideration and courtesy to others.
They will listen to other people's opinions respectfully.
These people will inspire others to share thoughts and feelings.
Additionally, the company culture encourages open communication as well as collaboration.
People feel comfortable expressing their opinions freely without fear of reprisal.
They know that they will not be judged if they make mistakes, as long as the matter is dealt with honestly.
The company culture promotes honesty, integrity, and fairness.
Everybody knows they have to tell the truth.
Everyone understands that there are rules and regulations which apply to them.
Everyone does not expect to receive special treatment.
It seems so difficult sometimes to make sound business decisions.
Complex systems with many moving parts are the hallmark of businesses. The people who run them must juggle multiple priorities at once while also dealing with uncertainty and complexity.
Understanding how these factors impact the whole system is key to making informed decisions.
This requires you to think about the purpose and function of each component. It is important to then consider how the individual pieces relate to each other.
You need to ask yourself if your previous actions have led you to make unfounded assumptions. If so, it might be worth reexamining them.
Asking for assistance from someone else is a good idea if you are still having trouble. They might see things differently than you and may have some insights that could help find a solution.
What is the difference between TQM and Six Sigma?
The main difference in these two quality management tools lies in the fact that six sigma is focused on eliminating defects and total quality management (TQM), emphasizes improving processes and reducing costs.
Six Sigma stands for continuous improvement. It emphasizes the elimination or minimization of defects through statistical methods such control charts and p charts.
This method seeks to decrease variation in product output. This is done by identifying root causes and rectifying them.
Total quality management involves measuring and monitoring all aspects of the organization. It also includes the training of employees to improve performance.
It is frequently used as an approach to increasing productivity.
What are the four major functions of Management?
Management is responsible of planning, organizing, leading, and controlling people as well as resources. It includes creating policies and procedures, as well setting goals.
Management assists an organization in achieving its goals by providing direction, coordination and control, leadership, motivation, supervision and training, as well as evaluation.
These are the four major functions of management:
Planning - Planning is about determining what must be done.
Organizing: Organizing refers to deciding how things should work.
Direction - This is the art of getting people to follow your instructions.
Controlling - Controlling means ensuring that people carry out tasks according to plan.
What are the most common errors made by managers?
Managers sometimes make their own job harder than necessary.
They may not assign enough responsibilities to staff members and provide them with inadequate support.
Additionally, many managers lack communication skills that are necessary to motivate and direct their teams.
Managers can set unrealistic expectations for their employees.
Managers might try to solve every problem by themselves rather than delegating the responsibility.
Statistics
- The profession is expected to grow 7% by 2028, a bit faster than the national average. (wgu.edu)
- Our program is 100% engineered for your success. (online.uc.edu)
- Your choice in Step 5 may very likely be the same or similar to the alternative you placed at the top of your list at the end of Step 4. (umassd.edu)
- The BLS says that financial services jobs like banking are expected to grow 4% by 2030, about as fast as the national average. (wgu.edu)
- 100% of the courses are offered online, and no campus visits are required — a big time-saver for you. (online.uc.edu)
External Links
How To
How is Lean Manufacturing done?
Lean Manufacturing techniques are used to reduce waste while increasing efficiency by using structured methods. They were created in Japan by Toyota Motor Corporation during the 1980s. It was designed to produce high-quality products at lower prices while maintaining their quality. Lean manufacturing eliminates unnecessary steps and activities from a production process. It includes five main elements: pull systems (continuous improvement), continuous improvement (just-in-time), kaizen (5S), and continuous change (continuous changes). The production of only what the customer needs without extra work is called pull systems. Continuous improvement is the continuous improvement of existing processes. Just-in time refers to components and materials being delivered right at the place they are needed. Kaizen means continuous improvement. Kaizen involves making small changes and improving continuously. Last but not least, 5S is for sort. These five elements are combined to give you the best possible results.
Lean Production System
The lean production system is based on six key concepts:
-
Flow: The goal is to move material and information as close as possible from customers.
-
Value stream mapping- This allows you to break down each step of a process and create a flowchart detailing the entire process.
-
Five S's: Sort, Shine Standardize, Sustain, Set In Order, Shine and Shine
-
Kanban: Use visual signals such stickers, colored tape, or any other visual cues, to keep track your inventory.
-
Theory of Constraints - Identify bottlenecks in the process, and eliminate them using lean tools such kanban boards.
-
Just-in time - Get components and materials delivered right at the point of usage;
-
Continuous improvement: Make incremental improvements to the process instead of overhauling it completely.