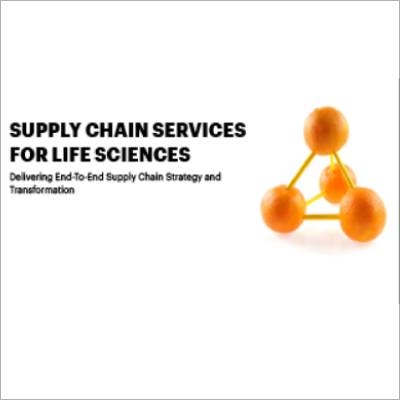
An ISO document contains many rules that are vital for readers to understand. For example, abbreviations must be precise and unambiguous. Certain forms of punctuation should be avoided. These include symbols to indicate quantities and language. These guidelines will make it easier and more intuitive for readers to read the ISO document.
Forms
The implementation of electronic ISO documents forms can help improve customer satisfaction, regulatory compliance, quality, and company processes. Remember to keep these forms simple, break them down into data types, and ensure they are part or a larger process. Agile development is essential. Users' requirements should be gathered early. User testing is also a good idea. This can help you discover issues that you didn't anticipate. It is also important to provide training for all software-specific users.
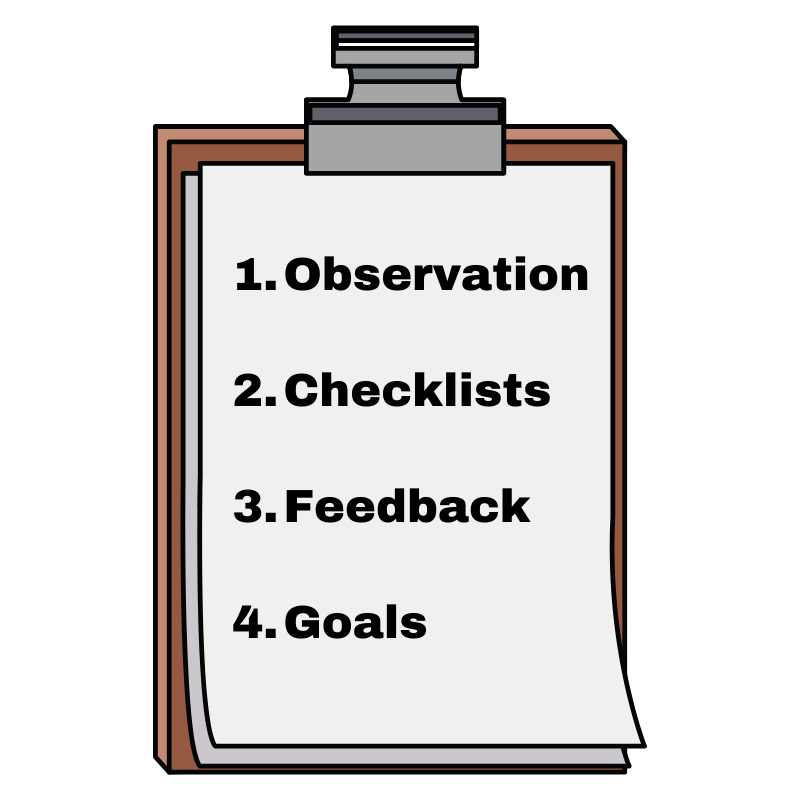
Symbols for quantities
In ISO documents, numbers are represented using symbols. These symbols are usually abbreviated terms, and are generally written in italics, unlike words or numbers that are written in lowercase. There are some abbreviations that have special meanings such as "net present value" or "internal rateof return". The standard also provides guidelines for the types of symbols that can be used to indicate quantities.
Acronyms
Most people are familiar with some common acronyms, especially if they read ISO documents regularly. CAR stands for Corrective Activity Request. This acronym is used to refer to any activity that results in Corrective Action (CA). This usually involves investigating a problem, identifying the root cause and preventing it from recurring. This can be used to describe the entire Corrective Action cycle.
Language
It is crucial that the language of ISO documents is understood by the intended audience. There are certain conventions that characterize this language. Abbreviations are commonly used, but only the first word of a term is capitalized. For radio frequency, however, it is not acceptable to use the abbreviation d.c.
Formatting
Documentation is an integral part of ISO standards. Some organizations are too detailed, which can lead to inflexibility. This problem can be avoided by ensuring that your documentation is in the right structure and style.
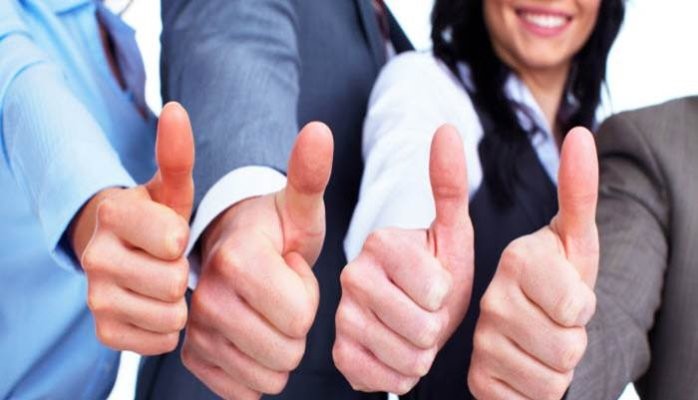
Publishing
ISO publishes documents in different formats. ISO documents are called ISO standards or IEC standards. They are the product of the ISO/IEC JTC 1 and American Society for Testing and Materials. ISO standards do not always match ASTM standards. Some standards may not be complete and therefore are not published. This is why their designation is often left out in the title of published works.
FAQ
What is the best way to motivate your employees as a manager?
Motivation refers to the desire or need to succeed.
It is possible to be motivated by doing something you enjoy.
You can also feel motivated by making a positive contribution to the success in the organization.
For example, if your goal is to become a physician, you will probably find it more motivational to see patients rather than to read a lot of medicine books.
The inner motivation is another type.
For example, you might have a strong sense of responsibility to help others.
Or you might enjoy working hard.
Ask yourself why you aren't feeling motivated.
Then try to think about ways to change your situation to be more motivated.
What are the most common errors made by managers?
Sometimes, managers make their job more difficult than it is.
They may not be able to delegate enough responsibility to staff or provide adequate support.
A majority of managers lack the communication skills needed to motivate their team and lead them.
Some managers set unrealistic expectations for their staff.
Managers may prefer to solve every problem for themselves than to delegate responsibility.
What's the difference between a program and a project?
A program is permanent while a project can be temporary.
A project is usually defined by a clear goal and a set deadline.
This is often done by a group of people who report to one another.
A program usually has a set of goals and objectives.
It is often implemented by one person.
What is Six Sigma, exactly?
It's an approach to quality improvement that emphasizes customer service and continuous learning. This is an approach to quality improvement that uses statistical techniques to eliminate defects.
Motorola invented Six Sigma in 1986 as part its efforts to improve manufacturing.
It was quickly adopted by the industry and many companies are now using six-sigma to improve product design, production, delivery, customer service, and product design.
What are the five management steps?
Each business has five stages: planning, execution and monitoring.
Planning involves setting goals for the future. It involves setting goals and making plans.
Execution is the actual execution of the plans. These plans must be adhered to by everyone.
Monitoring is a way to track progress towards your objectives. Regular reviews of performance against targets, budgets, and other goals should be part.
Reviews take place at the end of each year. They are a chance to see if everything went smoothly during the year. If not then, you can make changes to improve your performance next year.
After each year's review, evaluation occurs. It helps to identify what went well and what didn’t. It also provides feedback on how well people performed.
Statistics
- The BLS says that financial services jobs like banking are expected to grow 4% by 2030, about as fast as the national average. (wgu.edu)
- 100% of the courses are offered online, and no campus visits are required — a big time-saver for you. (online.uc.edu)
- As of 2020, personal bankers or tellers make an average of $32,620 per year, according to the BLS. (wgu.edu)
- The average salary for financial advisors in 2021 is around $60,000 per year, with the top 10% of the profession making more than $111,000 per year. (wgu.edu)
- This field is expected to grow about 7% by 2028, a bit faster than the national average for job growth. (wgu.edu)
External Links
How To
How does Lean Manufacturing work?
Lean Manufacturing techniques are used to reduce waste while increasing efficiency by using structured methods. These processes were created by Toyota Motor Corporation, Japan in the 1980s. The main goal was to produce products at lower costs while maintaining quality. Lean manufacturing seeks to eliminate unnecessary steps and activities in the production process. It is made up of five elements: continuous improvement, continuous improvement, just in-time, continuous change, and 5S. Pull systems are able to produce exactly what the customer requires without extra work. Continuous improvement is constantly improving upon existing processes. Just-in–time refers when components or materials are delivered immediately to their intended destination. Kaizen means continuous improvement. Kaizen involves making small changes and improving continuously. The 5S acronym stands for sort in order, shine standardize and maintain. To achieve the best results, these five elements must be used together.
Lean Production System
The lean production system is based on six key concepts:
-
Flow: The goal is to move material and information as close as possible from customers.
-
Value stream mapping: This is a way to break down each stage into separate tasks and create a flowchart for the entire process.
-
Five S's - Sort, Set In Order, Shine, Standardize, and Sustain;
-
Kanban is a visual system that uses visual cues like stickers, colored tape or stickers to keep track and monitor inventory.
-
Theory of constraints: Identify bottlenecks and use lean tools such as kanban boards to eliminate them.
-
Just-in time - Get components and materials delivered right at the point of usage;
-
Continuous improvement is making incremental improvements to your process, rather than trying to overhaul it all at once.