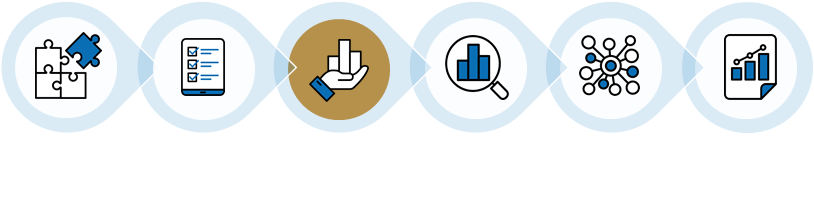
The certificate program in construction management can help you to be a leader within the field. The cutting-edge curriculum equips students with essential skills necessary in today's fast-paced construction industry. Construction law, scheduling and BIM are all topics that students can study. Students will be able to build leadership and interpersonal skills. A certificate in construction management is the best way for you to get started, regardless of whether your goal is to open your own company or work in the construction industry.
Coursework
Construction management certificates are designed to increase the skills of project managers. It covers topics such as project planning, scheduling, budgeting, manpower allocation, and code compliance. The course also covers topics like the critical path method, scheduling tools, and other relevant topics. The student will also learn about the importance of Cash Flow Diagrams. This course is required if you are interested in working in the construction industry.
A student must complete all courses within four years of admittance to the U of M in order to be awarded a construction manager certificate. The average student must earn a C or have an overall GPA of at least 2. The certificate can be awarded concurrently to an undergraduate degree. The program is open to individuals who have previous experience in the building industry. However, students must apply for admission as soon as they can.
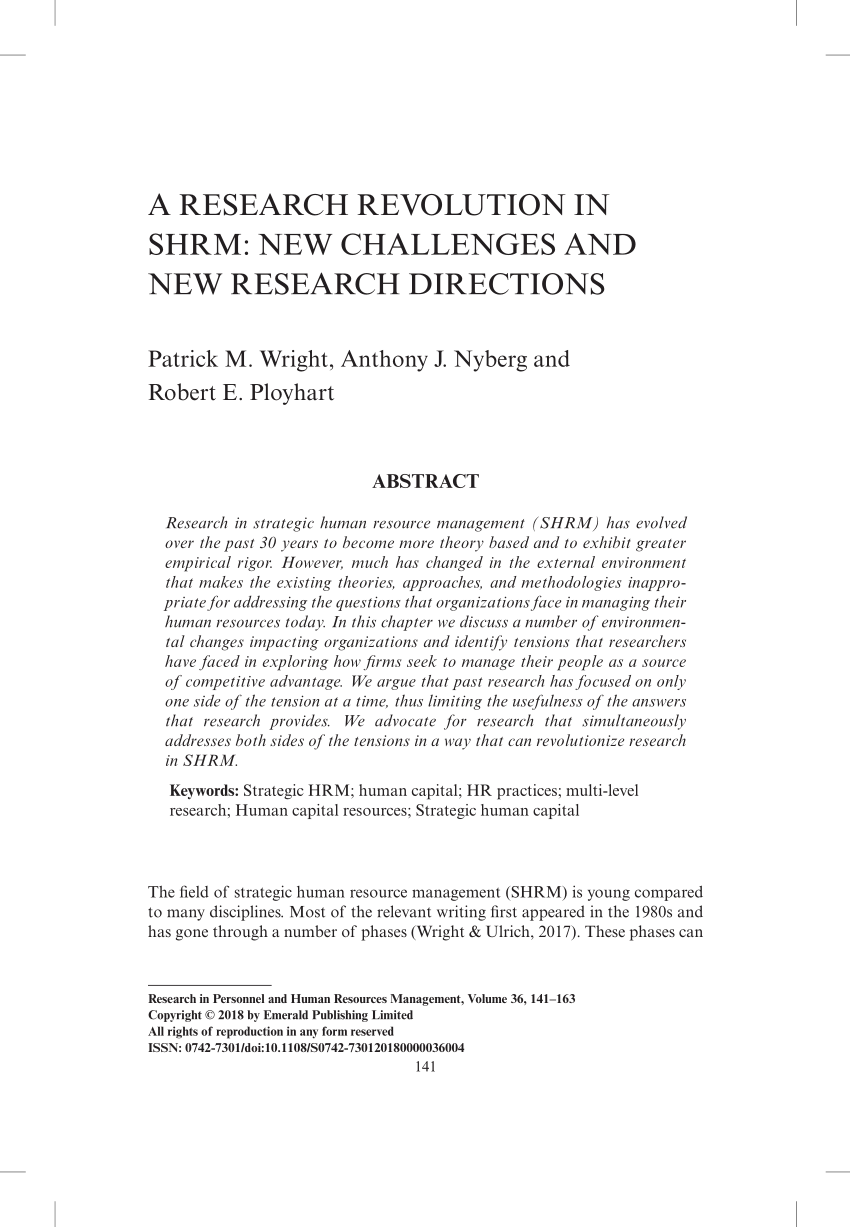
Credentials
A certificate in construction management is an important credential that you can have if you want to work in construction. Employers will be impressed by your commitment to this career. This certification is a professional advantage for those looking to start a business or work as a freelancer in this field. There are many colleges and universities that offer certificates in construction management. There is constant change in the construction industry, so it is highly desirable to have the skills that will make you a successful contractor.
Construction certifications can be beneficial for everyone involved in the building process. These programs can improve the professional practices of each individual, as well as the brand and quality of the workers' services. These programs also show that workers are skilled in the construction industry. This certification will allow you to earn a higher rate of pay for your services. Many cities across the country are hiring people in the construction field and a construction certification is an excellent way to stand out from the competition.
Requirements
While earning a certificate as a construction manager may not lead you to employment, it can increase your job prospects. Typically, students who complete a certificate program gain knowledge in project delivery, building information modeling, and decision-making. Certificate programs generally last two years and don’t require any extra coursework. A certificate program can help you develop your professional skills by allowing you to demonstrate your knowledge in your field. It is not necessary to be an industry expert to earn a certificate.
A certificate that is exam-like is also possible. This type of certificate is available for between $500 to $1,100. You will need to pass a final examination. You will pay for the certificate once you pass the exam, so make sure you can afford the cost. The requirements for earning a certification will vary depending on the level of your education and your employer's requirements. You should learn as much as you can about each option before making a decision to pursue one.
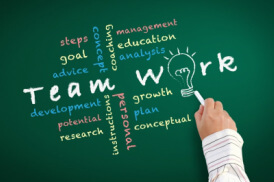
Online programs
A certificate in construction management can be earned online, which will help you stand out among other job candidates. This certificate will show employers that your ability to take on a high-level job in a construction firm. Ashworth College offers online programs for construction management certificates at competitive tuition rates. The links below will take you to more information about the program. We hope you find the following information helpful. Construction is highly competitive. Earning your online certificate in construction management will help you get that job.
You can earn a certificate in construction management to be more efficient in managing employees and coordination of projects. The course offers cutting edge curriculum in project planning, scheduling, BIM and construction law. It also helps to develop leadership and interpersonal skills. This program is great for people who are interested in a career in construction but don't have enough time or education.
FAQ
What are the most common errors made by managers?
Managers can make their jobs more difficult than necessary.
They may not delegate enough responsibilities to staff and fail to give them adequate support.
Additionally, many managers lack communication skills that are necessary to motivate and direct their teams.
Managers sometimes set unrealistic expectations of their teams.
Managers may attempt to solve all problems themselves, rather than delegating it to others.
What are the most important management skills?
Business owners need to have management skills, no matter how small or large they may be. These skills include the ability manage people, finances and resources as well as other factors.
You will need management skills to set goals and objectives, plan strategies, motivate employees, resolve problems, create policies and procedures, and manage change.
There are so many managerial tasks!
What kind people use Six Sigma?
Six-sigma will be well-known to anyone who has worked in operations research or statistics. Anyone involved in business can benefit.
It requires high levels of commitment and leadership skills to be successful.
What is the main difference between Six Sigma Six Sigma TQM and Six Sigma Six Sigma?
The main difference between these two quality management tools is that six sigma focuses on eliminating defects while total quality management (TQM) focuses on improving processes and reducing costs.
Six Sigma is a method for continuous improvement. It emphasizes the elimination of defects by using statistical methods such as control charts, p-charts, and Pareto analysis.
This method aims to reduce variation in product production. This is accomplished through identifying and correcting root causes.
Total quality management refers to the monitoring and measurement of all aspects in an organization. Training employees is also part of total quality management.
It is often used as a strategy to increase productivity.
What are the five management processes?
Each business has five stages: planning, execution and monitoring.
Setting goals for the future is part of planning. This includes setting goals for the future and defining what you want.
Execution occurs when you actually carry out the plans. These plans must be adhered to by everyone.
Monitoring allows you to monitor your progress towards achieving your goals. This should involve regular reviews of performance against targets and budgets.
Every year, there are reviews. They are a chance to see if everything went smoothly during the year. If not, it is possible to make improvements for next year.
After the annual review, evaluation takes place. It helps you identify the successes and failures. It also provides feedback on the performance of people.
What are management concepts?
Management Concepts are the principles and practices managers use to manage people and resources. They include such topics as human resource policies, job descriptions, performance evaluations, training programs, employee motivation, compensation systems, organizational structure, and many others.
What is a fundamental management tool for decision-making?
A decision matrix is a simple but powerful tool for helping managers make decisions. They can think about all options and make informed decisions.
A decision matrix represents alternatives in rows and columns. It is easy to see how each option affects the other options.
We have four options in this example. They are represented by the boxes to the left of the matrix. Each box represents one option. The top row shows the status quo (the current situation), and the bottom row shows what would happen if nothing was done at all.
The effect of selecting Option 1 is shown in the middle column. In this example, it would lead to an increase in sales of between $2 million and $3 million.
These are the results of selecting Options 2 or 3. These are positive changes - they increase sales by $1 million and $500 thousand respectively. But, they also have some negative consequences. Option 2 can increase costs by $100 million, while Option 3 can reduce profits by $200,000.
The final column shows the results for Option 4. This results in a decrease of sales by $1,000,000
The best thing about using a decision matrix is that you don't need to remember which numbers go where. The best thing about a decision matrix is that you can simply look at the cells, and immediately know whether one option is better or not.
This is because the matrix has already taken care of the hard work for you. It's simply a matter of comparing the numbers in the relevant cells.
Here is an example how you might use the decision matrix in your company.
Advertising is a decision that you make. This will allow you to increase your revenue by $5000 per month. You'll also have additional expenses up to $10,000.
The net result of advertising investment can be calculated by looking at the cell below that reads "Advertising." It is 15 thousand. Therefore, you should choose to invest in advertising since it is worth more than the cost involved.
Statistics
- Hire the top business lawyers and save up to 60% on legal fees (upcounsel.com)
- Your choice in Step 5 may very likely be the same or similar to the alternative you placed at the top of your list at the end of Step 4. (umassd.edu)
- 100% of the courses are offered online, and no campus visits are required — a big time-saver for you. (online.uc.edu)
- The average salary for financial advisors in 2021 is around $60,000 per year, with the top 10% of the profession making more than $111,000 per year. (wgu.edu)
- As of 2020, personal bankers or tellers make an average of $32,620 per year, according to the BLS. (wgu.edu)
External Links
How To
How is Lean Manufacturing done?
Lean Manufacturing uses structured methods to reduce waste, increase efficiency and reduce waste. They were created in Japan by Toyota Motor Corporation during the 1980s. It was designed to produce high-quality products at lower prices while maintaining their quality. Lean manufacturing eliminates unnecessary steps and activities from a production process. It is composed of five fundamental elements: continuous improvement; pull systems, continuous improvements, just-in–time, kaizen, continuous change, and 5S. The production of only what the customer needs without extra work is called pull systems. Continuous improvement means continuously improving on existing processes. Just-in time refers to components and materials being delivered right at the place they are needed. Kaizen stands for continuous improvement. Kaizen can be described as a process of making small improvements continuously. The 5S acronym stands for sort in order, shine standardize and maintain. These five elements are combined to give you the best possible results.
The Lean Production System
The lean production system is based on six key concepts:
-
Flow - The focus is on moving information and material as close as possible to customers.
-
Value stream mapping is the ability to divide a process into smaller tasks, and then create a flowchart that shows the entire process.
-
Five S's - Sort, Set In Order, Shine, Standardize, and Sustain;
-
Kanban is a visual system that uses visual cues like stickers, colored tape or stickers to keep track and monitor inventory.
-
Theory of constraints - identify bottlenecks in the process and eliminate them using lean tools like kanban boards;
-
Just-in-time - deliver components and materials directly to the point of use;
-
Continuous improvement - make incremental improvements to the process rather than overhauling it all at once.